INSPIRE project goal is nanometer-accurate shape and position sensors
Germany counts high-precision manufacturing processes among its advantages. To retain this technological edge, many companies process metal components to the exact micrometer with zero waste. It's not just the aerospace and automotive industries that require almost waste-free, high-precision manufacturing in the micrometer range to provide an energy- and resource-efficient way of testing the shape and orientation tolerances of products during the manufacturing process. Since current inline measurement technology does not yet provide the required accuracy, the Fraunhofer Institute for Laser Technology (Fraunhofer ILT; Aachen, Germany) is collaborating with four renowned industry partners in the INSPIRE project—Interferometric Distance Sensors with Automated Subsystems for Precision Inline Measurement to Regulate Automated Manufacturing Processes—to develop inline sensors with a new accuracy class. Funded by the German Federal Ministry of Education and Research (BMBF), the project is scheduled to run until the end of 2019.
RELATED ARTICLE: Subaperture stitching interferometry enhances advanced freeform optics
Sensors that can work precisely and reliably even under unfavorable conditions are paramount to monitoring and regulating high-precision manufacturing processes. Interferometers are used under laboratory conditions to measure the shape of components with the highest precision; for example, thickness of sheet metal, roundness of rollers, and eccentricity of waves. In fact, Interferometers are so precise that they can be used to determine not just the component’s shape but also its surface roughness.
To this end, an interferometer's settings must be adapted precisely to the measurement task at hand. This especially requires correct exposure time and focus; similar to taking a photo. In April this year, the collaborative project INSPIRE was started with the aim of developing an interferometer that can adapt to varying measuring conditions. "The sensors will have digitized expert knowledge and can autonomously optimize the settings," says Hölters from Fraunhofer ILT in Aachen. He coordinates the INSPIRE project, in which four other small and medium-sized enterprises are participating. With the development of fast control electronics, the sensors can adapt to rapidly changing measuring conditions within microseconds. This development will benefit conventional processes such as the cold rolling of sheet metal as well as machining processes such as welding.
The BMBF has pledged half the funding for the three-year long collaborative project as part of the "Digital Optics" funding initiative. Companies participating in the INSPIRE project are LSA or Laser Analytical Systems & Automation and Beratron (both in Aachen, Germany), HIGHYAG Lasertechnologie (Kleinmachnow, Germany), and Friedrich Vollmer Feinmessgerätebau (Hagen, Germany).
SOURCE: Fraunhofer ILT; http://www.ilt.fraunhofer.de/en/press/press-releases/PR2017/press-release-2017-06-13.html
About the Author
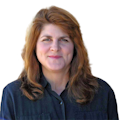
Gail Overton
Senior Editor (2004-2020)
Gail has more than 30 years of engineering, marketing, product management, and editorial experience in the photonics and optical communications industry. Before joining the staff at Laser Focus World in 2004, she held many product management and product marketing roles in the fiber-optics industry, most notably at Hughes (El Segundo, CA), GTE Labs (Waltham, MA), Corning (Corning, NY), Photon Kinetics (Beaverton, OR), and Newport Corporation (Irvine, CA). During her marketing career, Gail published articles in WDM Solutions and Sensors magazine and traveled internationally to conduct product and sales training. Gail received her BS degree in physics, with an emphasis in optics, from San Diego State University in San Diego, CA in May 1986.