Tailored photoacoustic elements create patterned ultrasound fields
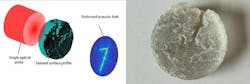
Limitations of piezoelectric array technologies conventionally used for ultrasonics inspired a group of researchers at University College London (England) to explore an alternative mechanism for generating ultrasound via the photoacoustic effect.1 Coupling this with 3D printing, the group was able to generate sound fields with specific shapes for potential use in biological cell manipulation and drug delivery.
Piezoelectric materials generate mechanical stress in response to an applied electric field, resulting in a usable and precisely controllable force that can be used to create sound waves. But achieving this control with conventional piezoelectric arrays requires both complicated electronics and large numbers of very small individual components, which are expensive and difficult to manufacture.
The photoacoustic effect, in contrast, occurs when a short pulse or modulated source of light is absorbed by a material, producing a sound wave. The researchers' new work focuses on using the photoacoustic effect to control ultrasound fields in 3D.
"One useful feature of the photoacoustic effect is that the initial shape of the sound that’s generated is determined [by] where the light is absorbed," says Michael Brown, a doctoral student at the Biomedical Ultrasound Group of the Department of Medical Physics and Biomedical Engineering at University College London. "This can be used to create tightly focused intense points of sound just by depositing an optical absorber on a concave surface, which acts like a lens."
3D printed transparent material
More generally, it’s possible to manufacture samples with nearly any surface shape by using a 3D printer and a transparent material.
"By depositing an optical absorber on this surface, which can be done via spray painting, a sound wave of nearly any shape can be created by illuminating this sample with a laser," Brown says. "If you carefully tailor the design of the surface and therefore the shape of the acoustic wave, it’s possible to control where the sound field will focus and even create fields focused over continuous shapes. We’re using letters and numbers."
The group "developed an algorithm that allows users to input a desired sound field in 3D, and it then outputs a 3D printable surface profile that generates this field," Brown says. "Our algorithm allows for precise control of the intensity of sound at different locations and the time at which the sound arrives, making it quick and easy to design surfaces or 'lenses' for a desired application."
Brown and his colleagues demonstrated the effectiveness of their algorithm by 3D-printing a transparent plastic lens designed to generate a sound field shaped like the numeral 7. After illuminating the lens by a pulsed laser (a fiber-coupled Q-switched Nd:YAG laser emitting at 1064 nm) with a tophat intensity profile, they recorded the sound field and the desired "7" was clearly visible with high contrast.
There are many potential uses for the tailored optoacoustic profiles created by the group. "Highly intense sound can cause heating or exert forces on objects, such as in acoustic tweezers," Brown says. "And similar single-focus devices are already being used for cleaving cell clusters and targeted drug delivery, so our work could be useful within that area."
The group is also interested in the effects of propagating through tissue, which introduces distortions to the shape of wavefronts caused by variations in the speed of sound. "If the structure of the tissue is known beforehand via imaging, our approach can be used to correct for these aberrations," says Brown.
Going forward, Brown and his group hope to investigate the use of other light sources, such as modulated light sources, and what advantages they might offer.
REFERENCE:
1. M. D. Brown et al., Applied Physics Latters 110, 094102 (2017); doi: http://dx.doi.org/10.1063/1.4976942
About the Author
John Wallace
Senior Technical Editor (1998-2022)
John Wallace was with Laser Focus World for nearly 25 years, retiring in late June 2022. He obtained a bachelor's degree in mechanical engineering and physics at Rutgers University and a master's in optical engineering at the University of Rochester. Before becoming an editor, John worked as an engineer at RCA, Exxon, Eastman Kodak, and GCA Corporation.