IPG Photonics and Brose partner on laser weld measurement technology
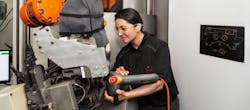
Fiber laser manufacturer IPG Photonics (Oxford, MA) and automotive mechatronics supplier The Brose Group (Auburn Hills, MI) announced a project to collaborate on the development of the first direct-weld measurement technology for automotive seat rails.
In-line coherent imaging (ICI) technology will increase manufacturing efficiency, streamline validation, and minimize waste. After piloting the state-of-the-art laser welding technology in its London, ON, Canada facility, Brose will integrate weld cells into several manufacturing facilities in the US and Europe, with production set to begin early 2020.
“Projects like this with leading technology providers allow Brose to incorporate the most advanced production processes, such as direct weld measurement, and help us continue advancing new breakthroughs in seat structures. This differentiator allows us to remain an industry leader while, ultimately, increasing our customer’s confidence and satisfaction with our products,” said Stefan Krug, COO, Brose North America.
The ICI technique is a sophisticated welding technology due to its ability to increase manufacturing efficiency through simplified validation. The process also tracks seams to detect surface irregularities and ensure weld quality, replacing an indirect measurement approach that requires a one-hour validation process that pauses production.
“Our patented, in-line welding monitoring tools provide the most comprehensive and direct measurement of key manufacturing characteristics including weld depth, part fit-up and seam position,” said Trevor Ness, IPG Photonics SVP worldwide sales & marketing. “IPG is proud to put our laser depth monitoring technology to work with Brose to support producing the highest quality seat rails available to consumers.”
Brose plans to invest more than $6 million by 2022 to develop the technology. As part of this project, Brose and IPG Photonics will study and analyze ICI generated performance data including penetration measurements, surface irregularities, seam tracking and the technical availability of the equipment. This joint project will help inform further manufacturing efficiencies, consumer safety and performance enhancements to improve the overall quality of products reaching consumers in the marketplace.
Brose is a leader in mechatronics--the integration of mechanics, electronics, and sensors--and a major manufacturer of seat structures to the global automotive industry. In 2018, the company produced more than 80 million seat rails globally and expects to manufacture more than 105 million annually by 2024.
SOURCE: Brose North America; https://www.brose.com/us-en/press/brose-collaborates-with-ipg-photonics-on-advanced-laser-welding-technology-for-automotive-seat-structures.html
About the Author
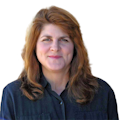
Gail Overton
Senior Editor (2004-2020)
Gail has more than 30 years of engineering, marketing, product management, and editorial experience in the photonics and optical communications industry. Before joining the staff at Laser Focus World in 2004, she held many product management and product marketing roles in the fiber-optics industry, most notably at Hughes (El Segundo, CA), GTE Labs (Waltham, MA), Corning (Corning, NY), Photon Kinetics (Beaverton, OR), and Newport Corporation (Irvine, CA). During her marketing career, Gail published articles in WDM Solutions and Sensors magazine and traveled internationally to conduct product and sales training. Gail received her BS degree in physics, with an emphasis in optics, from San Diego State University in San Diego, CA in May 1986.