NIST research to improve viability and marketability of laser welding
IMAGE: Inside NIST's laser welding booth, a high-power laser melts a piece of metal to form the letters NIST. (Image credit: Paul Williams/NIST)
Researchers say the physics of laser welding is surprisingly complex. A better understanding of the interaction between laser and metal could give industry more control over laser welding, a technology that is becoming increasingly popular in manufacturing. For the past three years, scientists at the National Institute of Standards and Technology (NIST) have been collecting data on the most fundamental aspects of laser welding. The scope of their study is narrow, but the measurements of this complicated process are more accurate and comprehensive than any data ever collected on the subject, the researchers say.
Now, this information is starting to be used by computer modelers to improve simulations of laser welding processes, a necessary step to prepare the work for industry.
"Our results are now mature enough to where academic researchers are starting to use our data to thoroughly test their computer models in a way that they just haven’t been able to do before, because this kind of data hasn’t been available," said NIST physicist Brian Simonds.
Conventional welding typically uses an arc of electricity to heat and fuse materials. In contrast, a multi-kilowatt laser beam can heat a smaller area of the metals being joined, creating a smaller, smoother seam than a conventional weld, on the order of millimeters rather than centimeters. Laser welding is also faster and more energy-efficient than conventional welding, the researchers say.
Even with these and other advantages, laser welding makes up only a small fraction of overall welding efforts in the U.S. that might benefit from this technique. A better understanding of the process could make it easier for industries to consider investing in laser-welding infrastructure, the researchers say.
"The ultimate goal for industry is that one day, if you have an idea about something you want to make, you dump it into a computer and the computer tells you exactly how to make it," Simonds said. Though that ideal is a decade or more away, he continued, manufacturers may start seeing a benefit much sooner, as the NIST collaboration's progress helps refine the computer models. These simulations help manufacturers predict what kinds of welds they can expect with different settings.
To make the models, though, researchers need data from past experiments. And that research is spread across hundreds of studies, representing decades of work from dozens of laboratories. For example, they might find information about the heat capacity of one alloy in a paper from 1970, the thermal conductivity of a similar alloy in a paper from 1992, and experimental data on weld behavior from 2007. But piecing this information together requires introducing a lot of what Simonds called 'fudge factors'. "Modelers look through all these resources from different labs for different materials, and they kludge them together in a way that they think is most applicable to their experiment," Simonds said. "And they say, 'It's close enough.' But they don’t really know."
In contrast, the NIST team is attempting to build a much firmer foundation for a model. NIST researchers are measuring everything that a simulator would need--the amount of power that is hitting the metal, the amount of energy the metal is absorbing, the amount of material that is evaporating from the metal as it is heated--all in real time.
Many of the techniques the researchers are using to collect the data were either designed or developed at NIST to measure novel aspects of welding. For example, until recently researchers could not gauge laser power during a weld. NIST physicists John Lehman and Paul Williams and their colleagues designed and built a device that can accomplish this using the pressure of the light itself.
To solve this problem, they surrounded the metal sample with a device called an integrating sphere, designed to capture all the light bouncing off the metal. Using this technique, they discovered that the traditional method for making this measurement "severely underestimates" the energy absorbed by the metal during a laser weld. The integrating sphere also allows the data to be measured in real time.
They also found a way to better measure the weld plume, a cloud of vaporized materials that includes tiny amounts of elements that evaporate out of the sample during welding. To sense these minuscule signals, NIST researchers are adapting a technique called laser-induced fluorescence (LIF) spectroscopy. The method involves hitting the plume with a second laser that targets just one kind of element at a time. The targeted element absorbs the second laser's energy and then releases it at a slightly shifted energy, producing a strong signal that is also a unique marker of that element. So far, researchers have demonstrated that LIF can sense trace elements in the weld plume with 40,000 times more sensitivity than traditional methods.
Another important aspect of the work is that researchers are conducting all of their experiments with a type of stainless steel that is a NIST standard reference material (SRM), meaning its composition is extremely well known. Using the stainless-steel SRM ensures that experiments conducted anywhere in the world can have access to metal samples with an identical composition, so that everyone is effectively contributing to one big project.
As they continue to gather information, the NIST scientists are collaborating with institutes around the world to expand the dataset. This summer, they will collaborate with the U.S. Department of Energy's Argonne National Laboratory to take advantage of the lab's unique ability to do high-speed X-ray imaging of the molten pool of metal in real time. Other collaborators include Graz University of Technology in Austria, Queen’s University in Ontario, Canada, and the University of Utah in Salt Lake City.
Simonds and colleagues are also broadening the scope of their work as they direct their high-power laser beams onto metal powders instead of solids. The powder studies should directly support the community of additive manufacturing (a common form of 3D printing), whose market for products and services was worth more than an estimated $7.3 billion in 2017.
NIST researchers say the welding research project is a great opportunity for them to bring their physics chops to a complicated problem.
SOURCE: NIST; https://www.nist.gov/news-events/news/2019/04/nist-research-sparks-new-insights-laser-welding
About the Author
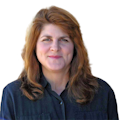
Gail Overton
Senior Editor (2004-2020)
Gail has more than 30 years of engineering, marketing, product management, and editorial experience in the photonics and optical communications industry. Before joining the staff at Laser Focus World in 2004, she held many product management and product marketing roles in the fiber-optics industry, most notably at Hughes (El Segundo, CA), GTE Labs (Waltham, MA), Corning (Corning, NY), Photon Kinetics (Beaverton, OR), and Newport Corporation (Irvine, CA). During her marketing career, Gail published articles in WDM Solutions and Sensors magazine and traveled internationally to conduct product and sales training. Gail received her BS degree in physics, with an emphasis in optics, from San Diego State University in San Diego, CA in May 1986.