Vegebot machine vision automates lettuce harvesting
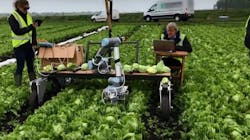
The ‘Vegebot’, developed by a team at the University of Cambridge in England, was initially trained to recognize and harvest iceberg lettuce in a lab setting. It has now been successfully tested in a variety of field conditions in cooperation with G’s Growers, a local fruit and vegetable co-operative.
Although the prototype is nowhere near as fast or efficient as a human worker, it demonstrates how the use of robotics in agriculture might be expanded, even for crops like iceberg lettuce which are particularly challenging to harvest mechanically. The results are published in The Journal of Field Robotics.
Crops such as potatoes and wheat have been harvested mechanically at scale for decades, but many other crops have to date resisted automation. Iceberg lettuce is one such crop. Although it is the most common type of lettuce grown in the UK, iceberg is easily damaged and grows relatively flat to the ground, presenting a challenge for robotic harvesters.
“Every field is different, every lettuce is different,” said co-author Simon Birrell from Cambridge’s Department of Engineering. “But if we can make a robotic harvester work with iceberg lettuce, we could also make it work with many other crops.”
“At the moment, harvesting is the only part of the lettuce life cycle that is done manually, and it’s very physically demanding,” said co-author Julia Cai, who worked on the computer vision components of the Vegebot while she was an undergraduate student in the lab of Fumiya Iida.
EDITOR’S NOTE: Living near Yuma, AZ, I am familiar first-hand with the process of lettuce harvesting, which is very difficult and requires a huge conveyer system. Robotics could automate the process and eliminate the controversial use of migrant labor.
The Vegebot first identifies the ‘target’ crop within its field of vision, then determines whether a particular lettuce is healthy and ready to be harvested, and finally cuts the lettuce from the rest of the plant without crushing it so that it is ‘supermarket ready’. “For a human, the entire process takes a couple of seconds, but it’s a really challenging problem for a robot,” said co-author Josie Hughes.
The Vegebot has two main components: a computer vision system and a cutting system. The overhead camera on the Vegebot takes an image of the lettuce field and first identifies all the lettuces in the image, and then for each lettuce, classifies whether it should be harvested or not. A lettuce might be rejected because it’s not yet mature, or it might have a disease that could spread to other lettuces in the harvest.
The researchers developed and trained a machine learning algorithm on example images of lettuces. Once the Vegebot could recognize healthy lettuces in the lab, it was then trained in the field, in a variety of weather conditions, on thousands of real lettuces.
A second camera on the Vegebot is positioned near the cutting blade and helps ensure a smooth cut. The researchers were also able to adjust the pressure in the robot’s gripping arm so that it held the lettuce firmly enough not to drop it, but not so firm as to crush it. The force of the grip can be adjusted for other crops.
In the future, robotic harvesters could help address problems with labor shortages in agriculture and could also help reduce food waste. Currently, each field is typically harvested once, and any unripe vegetables or fruits are discarded. However, a robotic harvester could be trained to pick only ripe vegetables, and since it could harvest around the clock, it could perform multiple passes on the same field, returning at a later date to harvest the vegetables that were unripe during previous passes.
Iida’s group at Cambridge is also part of the world’s first Centre for Doctoral Training (CDT) in agri-food robotics. In collaboration with researchers at the University of Lincoln and the University of East Anglia, the Cambridge researchers will train the next generation of specialists in robotics and autonomous systems for application in the agri-tech sector. The Engineering and Physical Sciences Research Council (EPSRC) has awarded million pounds for the new CDT, which will support at least 50 PhD students.
SOURCE: University of Cambridge; https://www.cam.ac.uk/research/news/robot-uses-machine-learning-to-harvest-lettuce
About the Author
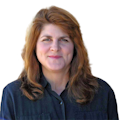
Gail Overton
Senior Editor (2004-2020)
Gail has more than 30 years of engineering, marketing, product management, and editorial experience in the photonics and optical communications industry. Before joining the staff at Laser Focus World in 2004, she held many product management and product marketing roles in the fiber-optics industry, most notably at Hughes (El Segundo, CA), GTE Labs (Waltham, MA), Corning (Corning, NY), Photon Kinetics (Beaverton, OR), and Newport Corporation (Irvine, CA). During her marketing career, Gail published articles in WDM Solutions and Sensors magazine and traveled internationally to conduct product and sales training. Gail received her BS degree in physics, with an emphasis in optics, from San Diego State University in San Diego, CA in May 1986.