Spectroscopy: Bowtie nanoapertures aid SEIRA spectroscopy of ultrafine particles
Ultrafine dust particles such as silica represent a health risk because of their ability to penetrate deep within lung tissue. To date, determining the size and chemical composition of ultrafine dust particles like silica with diameters of around 240 nm has been achieved using infrared (IR) spectroscopy by enhancing the phonon polariton signals of the particles using resonantly excited nanoslits.
Taking this technology a step further, researchers at the University of Heidelberg and the University of Stuttgart (both in Germany) have demonstrated chemical analysis of ultrafine particles with diameters as small as 34 nm using surface-enhanced infrared absorption (SEIRA) spectroscopy aided by plasmonic resonances of bowtie-shaped gold (Au) nanoapertures.1 Through numerical simulations, they have shown that the detection limit can be further improved to 15 nm by optimizing the bowtie geometry.
Nanoaperture particle confinement
Whether using fluorescence spectroscopy, surface-enhanced Raman spectroscopy (SERS), or SEIRA, the vibrational signal of molecules and particles is enhanced by using resonant plasmonic nanostructures such as linear and fan-shaped nanoantennas, nanoslits, or coupled nanostructures separated by a few nanometers. And while nanoslits have already shown promise in molecular spectroscopy of larger particles, the researchers were able to demonstrate through experiment and near-field simulations that they could optimize a bowtie-shaped nanoaperture to confine small-diameter spheres to enhance resonance.
Not only was the bowtie dimension optimized, but the process for confining a particle at the “hot spot” of the aperture (where the plasmon-polaritonic excitation of the bowtie structure and the phonon-polaritonic excitation of the particle overlap in both energy and volume) was simplified as well.
The bowties were fabricated on calcium fluoride (CaF2) crystals coated with 2.5 nm of chromium and 50 nm of gold using electron beam lithography. Subsequent argon-ion etching (in the shape of two triangles) was used to remove the coating as well as 15 nm of the CaF2 such that the indentation could precisely trap an 85-nm-diameter silica particle and no gold residual was left to short-circuit the aperture. The two triangles were separated by etched gaps that varied down to 20 nm.
To trap a particle in the center of an aperture, a dispersed mixture of 85-nm-diameter and smaller silica particles was pipetted onto the aperture, allowed to settle for 60 s, and then the aperture was spun for 60 s at 3000 rpm, trapping a particle in the tapered well at the center of the aperture while other particles are dispersed to the outside of the sample (see figure).
With a thermal source illuminating the bowtie and trapped silica sphere through a microscope objective, spectroscopic measurements were performed using a commercial Fourier transform IR spectrometer. By normalizing the reflectance of the bowtie nanoaperture to the bare gold substrate, relative reflectance was calculated. And by adding synchrotron radiation to the thermal source, measurement time could be reduced by a factor of 25 (the use of sophisticated light sources such as mid-IR lasers could further reduce measurement time).
Through simulations and measurements, the researchers found that the “hot spot” for resonance improved as a standard nanoslit was optimized into the bowtie shape, with the taper region optimized to match the diameter of the silica particle under test and allowing easier particle trapping. As the triangular base dimension increased, the vibrational signal strength of the illuminated particle increased by a factor of 3.5 to 7.8, with the deviation due to nonperfect positioning of a sphere at the center of the bowtie hot spot. In summary, the electromagnetic field enhancement at the center of the hot spot is maximized when the bowtie gap diameter and depth match the trapped particle size.
“Due to their large impact on environmental safety and health, fine and ultrafine particles with dimensions well below 100 nm are of special importance,” says Annemarie Pucci, professor at the University of Heidelberg. “As we have demonstrated, IR spectroscopy can identify such tiny particles if the extraordinary high electrical near-field enhancement of bowtie-shaped nanoapertures in metal films is exploited. We believe that our findings represent an important step for the characterization of ultrafine dust particles on a single particle level and opens new perspectives for dust sensing in numerous applications including dust from space exploration.”
REFERENCE
1. C. Huck et al., Phys. Rev. Appl., 11, 014036 (Jan. 18, 2019).
About the Author
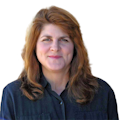
Gail Overton
Senior Editor (2004-2020)
Gail has more than 30 years of engineering, marketing, product management, and editorial experience in the photonics and optical communications industry. Before joining the staff at Laser Focus World in 2004, she held many product management and product marketing roles in the fiber-optics industry, most notably at Hughes (El Segundo, CA), GTE Labs (Waltham, MA), Corning (Corning, NY), Photon Kinetics (Beaverton, OR), and Newport Corporation (Irvine, CA). During her marketing career, Gail published articles in WDM Solutions and Sensors magazine and traveled internationally to conduct product and sales training. Gail received her BS degree in physics, with an emphasis in optics, from San Diego State University in San Diego, CA in May 1986.