Infrared Optics: Nonmechanical on-chip waveguide device steers mid-infrared beams
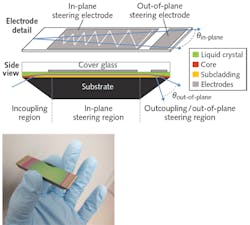
Mechanical devices for steering optical beams such as gimbal-mounted mirrors or rotating Risley prisms are subject to fatigue and mechanical breakdown, and also suffer from large size, weight, and power (SWaP) requirements. To avoid these drawbacks, researchers from the Naval Research Laboratory (NRL; Washington, DC) have devised a voltage-controlled, nonmechanical beam steering device that routes mid-wavelength infrared (MWIR or mid-IR) beams in two dimensions.1 This solid-state, mid-IR optical component relies on liquid-crystal-clad optical waveguides.
No moving parts
Compared to mechanical devices, the beauty of integrated optical components is their solid-state, rugged nature and amenability to miniaturization. And although other nonmechanical devices such as spatial light modulators (SLMs), optical phased arrays (OPAs), and polarization grating (PG) devices can provide beam steering, all of these are limited and operate in a fixed wavelength, with fixed steering angles, and/or limited power transmission capability.
Based on an architecture first proposed by Vescent Photonics (Boulder, CO), the NRL device is called a steerable electroevanescent optical refractor (SEEOR) and steers mid-IR beams continuously up to 14° in-plane and 0.6° out-of-plane in the 3–5 μm wavelength range.
To fabricate the SEEOR, multiple thin-film waveguide layers are first applied to a 48.5-mm-long, 14.5-mm-wide, faceted (3 mm long with 39º angle) 2.75-mm-thick doped-silicon substrate. The waveguide subcladding has a refractive index lower than either the substrate or the core and is tapered in the incoupling and outcoupling regions of the SEEOR (see figure). Light is coupled in or out of the faceted region of the slab waveguide in an Ulrich coupler configuration and travels to the core, which is comprised of chalcogenide glass (amorphous semiconductors that contain one or more of the “chalcogen” elements—sulfur, selenium, and tellurium—as a major constituent) of the formula arsenic selenide (As2Se3) with a higher refractive index than the arsenic sulfide (As2S3) subcladding. The core, subcladding, and substrate can transmit beams through the entire mid-IR spectrum.
The top cladding of the waveguide is a liquid crystal (LC) layer that resides between the core and an electrode-patterned cover glass. On top of the core as well as on the electrode side of the cover glass is a few-nanometer-thick LC alignment layer that induces the rod-shaped LC molecules to align. When a voltage is applied to the LC between the top electrode and the substrate, which serves as a bottom electrode, it causes the LC molecules to re-orient, changing the effective index in the waveguide and thus steering the beam.
To test the device operation, a 4.6 µm, 40 mW quantum-cascade laser (QCL), conditioned by collimating optics, was coupled in free space to the input facet of the SEEOR. The beam was captured by an infrared camera as voltage was applied to the in-plane and out-of-plane electrodes on the cover glass. Beam steering capabilities previously mentioned were confirmed through experimentation with steering voltages up to 500 V.
To increase the in-plane and out-of-plane steering capability and transmission, modifications can be made to the propagation length, facet angle optimization, electrode design modification, or the application of antireflective coatings on the face surfaces.
“Developing this MWIR beam-steering technology required us to solve a series of challenging problems—new waveguide designs and fabrication techniques, new LC compositions, new LC alignment techniques, all of which had to be compatible with MWIR light,” said Jesse Frantz, head of the NRL Specialty Waveguides Section. “We hope to see NRL’s MWIR SEEOR technology replace mechanical beam steerers, especially in situations where SWaP is a big concern. To give an example, consider a small UAV [unmanned aerial vehicle] surveying for methane leaks. It can’t carry a big payload, but steering a MWIR beam is critical for this application.”
REFERENCE
1. J. A. Frantz et al., J. Opt. Soc. Am. B, 35, 12, C29–C37 (2018).
About the Author
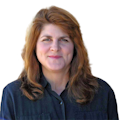
Gail Overton
Senior Editor (2004-2020)
Gail has more than 30 years of engineering, marketing, product management, and editorial experience in the photonics and optical communications industry. Before joining the staff at Laser Focus World in 2004, she held many product management and product marketing roles in the fiber-optics industry, most notably at Hughes (El Segundo, CA), GTE Labs (Waltham, MA), Corning (Corning, NY), Photon Kinetics (Beaverton, OR), and Newport Corporation (Irvine, CA). During her marketing career, Gail published articles in WDM Solutions and Sensors magazine and traveled internationally to conduct product and sales training. Gail received her BS degree in physics, with an emphasis in optics, from San Diego State University in San Diego, CA in May 1986.