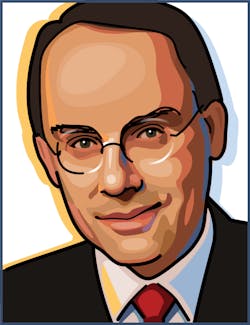
Do you remember when ultrafast lasers were complex setups and hard-to-align research systems? The progress they have made within the last 20 years is incredible. As Eric Mottay (Amplitude Systèmes) confirmed at this year's UKP workshop, their output power grew by a factor of 1000 and, most importantly, they became easy-to-handle industry-grade boxes. Now it's time to get them integrated into machines.
The UKP Workshop in Aachen, Germany is a small expert meeting where people think about all aspects of the industrial use of such lasers. UKP stands for the German "Ultrakurzpuls" or ultrashort pulsed. Held every other year, it drew 170 visitors from 14 countries this year. The program of the two-day meeting ranged from laser sources via scanners and optics to simulations, as well as applications of ultrafast-laser technology.One may think that everything has already been discussed about ultrafast laser sources, but last year, researchers at the Fraunhofer society announced their Cluster of Excellence "Advanced Photon Sources"—and this might be a game changer. As Dieter Hoffmann, one of the speakers of the project confirmed, they want to raise the power of ultrafast lasers to the levels at which continuous-wave (CW) lasers now do cutting and welding. In other words: "Femto goes macro!"
They are serious about it. After producing 3.5 kW from a fiber-laser system and, more recently, 500 W with a 30 fs pulse duration from a slab-laser system, the researchers want to launch two application labs, in Aachen and Jena, later this year to test new process technology with a number of their multikilowatt sources.
The crowd at the workshop just briefly touched upon the question of who would actually need thousands of watts of ultrafast laser radiation. However, not only have we had the same discussion in the past concerning fiber lasers and CO2 lasers, but the relevant point is that there are already first applications that clearly work well with high-power ultrafast lasers.
One example was shown by Stephan Brüning (Schepers GmbH). He uses a 500 W ultrafast laser source for processing of printing rollers. A few years ago, he was using four separate lasers to improve efficiency, but now with the new system he divides the high-power single laser beam into 16 beamlets, which are each controlled by an acousto-optic modulator. For the 1:16 division, he uses a diffractive optical element. Oskar Hofmann from Fraunhofer ILT has used the same technology to create almost 200 identical beamlets from one source. The main challenge here is to get all those beams through optics without introducing spatial distortions.
Ultrafast lasers for digital production systems
Reinhart Poprawe, the director of Fraunhofer ILT, worked hard for his vision of Digital Photonic Production. The laser is the perfect tool for a fully digital workflow, he often said. But is this yet realistic for ultrafast lasers?Claus Dold (EWAG AG) highlighted an example in which carbide and diamond drills are made with ultrafast lasers. The machine he presented is fully automated and needs geometrical data for the drill only. It selects appropriate laser parameters on its own and produces a set of drills. For diameters from 0.5 to 3 mm, the laser process is more efficient than other procedures. As a fully digital system, it is prepared to function within a global marketplace.
Even if such systems prove the feasibility of efficient production with ultrafast lasers, there remain a number of challenges now being addressed. Scanner technology either for high repetition rates or large bunches of beamlets is improving rapidly; simulation tools have improved by separating micro and macro levels; and even fibers for the transport of ultrafast laser radiation are now available.
Still, creating a machine for ultrafast lasers needs very detailed knowledge of the laser-matter interaction. And a relatively new safety concern arises in addition to laser-beam protection: ionizing radiation is regularly created by strong ultrafast pulses impinging on metal.
About the Author
Andreas Thoss
Contributing Editor, Germany
Andreas Thoss is the Managing Director of THOSS Media (Berlin) and has many years of experience in photonics-related research, publishing, marketing, and public relations. He worked with John Wiley & Sons until 2010, when he founded THOSS Media. In 2012, he founded the scientific journal Advanced Optical Technologies. His university research focused on ultrashort and ultra-intense laser pulses, and he holds several patents.