Fiber Sensing: Angled optical fiber end performs large-temperature-range sensing
Temperature sensing is ubiquitous in science, and both electronic and optical sensors are available. However, fiber-optic sensors offer immunity to electromagnetic interference and easy, flexible routing in remote-sensing applications.
State-of-the art fiber Bragg grating (FBG)-based temperature sensors offer 10 pm/°C sensitivity, but only operate over a range of temperatures from -200 to +150°C. Likewise, microstructured photonic-crystal fiber or hollow-core fiber sensors offer 18.7 pm/°C sensitivity, but only operate on the high end up to +460°C. Other alternatives that offer better sensitivity include whispering-gallery-mode and surface-plasmon-resonance sensors. Unfortunately, these options have limited temperature sensing range (usually from 0 to +100°C).
But a new fiber-optic sensing design from researchers at Tianjin University (Tianjin, China) uses a simple angled fiber end that relies on interferometric principles to achieve high sensitivity over a very broad range of temperatures from -40 to +140°C and 250 to 900°C, with sensitivity values that increase as temperature rises—specifically, 9.5 pm/°C at -40°C and 17.86 pm/°C at +900°C (see figure).1
Angled fiber interferometry
To fabricate the sensor, a standard Corning SMF-28 single-mode optical fiber with approximate 8.2-µm-diameter core and 125-µm-diameter cladding is inserted in a ceramic ferrule and polished to an angle of 60° from the original fiber surface. Since total internal reflection occurs at 43° for a silica/air interface according to Snell’s law, light that traverses through the fiber to its angled end is totally internally reflected, reaches the core/clad interface, and splits into two beams that then travel along different paths before recombining along the fiber core with an optical path difference that can be translated into a phase difference.
This angled end acts like a Michelson interferometer, producing fringes with a spacing of 7.5847 nm for a 1550 nm wavelength. And as the angled fiber end is exposed to temperature variations, thermal expansion of the fiber produces refractive-index changes and subsequent wavelength changes that correlate back to temperature.
The broad range of the sensor is because of the fact that the thermo-optic coefficient and thermal expansion coefficient of the fused silica optical fiber are constant and nonzero over a large temperature range. And the sensor is easily fabricated using standard optical-fiber polishing equipment and 1 µm diamond lapping film followed by a finer 0.3 µm diamond lapping film.
In the experimental setup, light from an amplified-spontaneous-emission (ASE) source with a spectral bandwidth of 1525 to 1605 nm was input to the fiber through a circulator, which also routes the reflected fiber signal to an optical spectrum analyzer (OSA) with a 0.05 nm resolution to measure the interference spectrum.
Temperature was controlled in the experiment in two different ranges by two different types of equipment: first, a Fluke 9171 metrology well temperature calibrator with a -45 to +155°C range and 0.01°C precision, and second, a Lindberg BF51866C Blue Moldatherm Box Furnace with range from 200 to 1100°C and 1°C precision. Experiments confirmed the 9.5 pm/°C and 17.86 pm/°C temperature-sensitivity values at the two extreme temperature ends of the range of -40 to +900°C.
REFERENCE
1. T. Wang et al., Opt. Fiber Technol., 45, 19–23 (2018).
About the Author
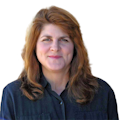
Gail Overton
Senior Editor (2004-2020)
Gail has more than 30 years of engineering, marketing, product management, and editorial experience in the photonics and optical communications industry. Before joining the staff at Laser Focus World in 2004, she held many product management and product marketing roles in the fiber-optics industry, most notably at Hughes (El Segundo, CA), GTE Labs (Waltham, MA), Corning (Corning, NY), Photon Kinetics (Beaverton, OR), and Newport Corporation (Irvine, CA). During her marketing career, Gail published articles in WDM Solutions and Sensors magazine and traveled internationally to conduct product and sales training. Gail received her BS degree in physics, with an emphasis in optics, from San Diego State University in San Diego, CA in May 1986.