Beyond industrial automation, the machine-vision industry is seeking new markets in areas such as transportation. Highway-safety-related applications often involve automated monitoring and enforcement. Yet another highway-safety application based on machine vision can monitor the actual condition of the roadway surface.
Road-surface analysis is conducted by departments of transportation as part of safety and quality checks of new roads and as part of inventory assessments of existing roadways. The smoothness of a road surface impacts many aspects of travel. For example, too much surface variance from the norm can result in an uneven ride, increased vehicle wear, a shortened road-surface lifetime, and safety concerns. Producing the correct road surface can affect as much as 5% of a multimillion-dollar paving contract.
The basic road-surface analysis procedure measures the smoothness of roads as a test vehicle drives the road at highway speed. The problem is complicated by the need to make surface measurements under uncontrolled lighting conditions and on surfaces that range from black asphalt to white concrete in varying environmental conditions.
In the past, engineers developed time-of-flight ultrasonic transmitters to measure the road’s smoothness or profile, but at travel speeds these systems could collect only one data point per foot. The next-generation system was a laser triangulation sensor, which bounced a single laser point off the road and collected the data. Pulsed-laser illumination with a fast read-out sensor enabled the second-generation system to collect data every millimeter, but only at one point.
The single-point system worked well on many surfaces, but when the road had longitudinal structures, such as grooves for greater traction, the laser point would wander in and out of the groove as the car drifted across the lane, yielding unrepeatable data. Asphalt roads have built-in texture because of the aggregate used, but for concrete roads a texture has to be created. In many cases the textures is longitudinal in nature, which is why this problem needs to be solved.
Lasing the road
Transportation engineers at the University of Michigan’s Transportation Research Center (UMTRI) recently tackled the problem using the Selcom RoLine sensor developed by LMI Technologies (Delta, BC, Canada). Laser-triangulation systems such as the RoLine generate height information along the z axis by projecting a flat laser line onto a surface, collecting an image of the line, and measuring the defection of the line from the horizontal norm. When properly calibrated and the stand-off distance determined, the distance the line varies from the norm directly translates to the surface height at that point.
The RoLine system generates up to 100 data points across the wheel path with submillimeter precision. The measurement data from the RoLine are combined with two external analog interfaces, an accelerometer for vehicle dynamics and an encoder for vehicle travel distance to achieve a true road profile. By moving from laser-point to laser-line illumination, this road profiler delivers 10 mm forward spatial resolution at highway speeds and provides 100 data points across a 100 mm width-or approximately the width of a standard automobile tire.
UMTRI tested the RoLine sensor as part of the American Concrete Pavement Association Profiler Repeatability Tests. The system, positioned in the wheel path in a test vehicle, included a red pulsed-laser-line generator at 660 nm with line-generating optics, a CMOS imager optimized for dynamic range, and custom optics to accommodate changes in focal depths as the car moved up and down as it traveled.
“The availability of line lasers for road profilers is a recent development,” said UMTRI’s Steve Karamihas. “It will provide us with the opportunity to write new standards for accuracy that ensure relevance of the measurements to end-user satisfaction-that is, vehicle dynamic response to road roughness.”
The existing system is mainly concerned with determining road height at any given point and how the frequency of movement impacts the natural frequency of a car’s vertical movement. Future improvements could include using multiple sensors and an improved network system to keep all devices in sync, including with the Global Positioning System.
About the Author
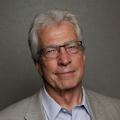
Conard Holton
Conard Holton has 25 years of science and technology editing and writing experience. He was formerly a staff member and consultant for government agencies such as the New York State Energy Research and Development Authority and the International Atomic Energy Agency, and engineering companies such as Bechtel. He joined Laser Focus World in 1997 as senior editor, becoming editor in chief of WDM Solutions, which he founded in 1999. In 2003 he joined Vision Systems Design as editor in chief, while continuing as contributing editor at Laser Focus World. Conard became editor in chief of Laser Focus World in August 2011, a role in which he served through August 2018. He then served as Editor at Large for Laser Focus World and Co-Chair of the Lasers & Photonics Marketplace Seminar from August 2018 through January 2022. He received his B.A. from the University of Pennsylvania, with additional studies at the Colorado School of Mines and Medill School of Journalism at Northwestern University.