Machine vision system with IDS Imaging camera reads Braille
Obersulm, Germany--A machine vision system that uses a USB camera from IDS Imaging Development GmbH insures that the Braille forms on important packaging such as medications is accurate and can be reliably read by the more than one million people in the United States alone that cannot read this text because they are blind. Braille, the method widely used by the visually impaired to read and write, uses a combination of up to six raised dots to represent every letter of the alphabet as well as numbers, musical notes, and many other symbols.
In the European Union, every medication package must provide key information about the product in Braille code since 2001. In the absence of a similar directive by the U.S. government, a new standard has been proposed by the International Association of Diecutting and Diemaking called "Can-Am-Braille" and derived from the European standard. According to the EU directive, at least the name and dosage of the medication has to be embossed on the folding box. However, meeting this requirement is not that easy. Even tiny faults in the manufacture of the folding boxes can have dangerous consequences. For example, just one raised dot that is too small or flat to be felt can be enough to cause unclear or even incorrect dosage information.
Although mechanical inspection systems have been used to assess the tactile quality of a Braille dot by measuring its height with fine micrometer screws, the method is time consuming and can damage the Braille dots by mechanical contact with the micrometer. But in-situ GmbH, a Munich based specialist for vision and sensor systems, has developed the DotScan inspection system to reliably recognize Braille dots and evaluate their tactile quality with high precision. Testing is non-contact using a state-of-the-art machine vision system and an industrial camera from IDS's USB uEye series. The monochrome CMOS camera captures 2D images. The height information is then calculated using a shape-from-shading algorithm. Lighting plays a key role in this process: To obtain accurate results, telecentric light sources are required, which illuminate the Braille embossed folding box from four directions at an angle from above. The telecentric light ensures that the 3D shape of a raised dot can be accurately derived from its shading pattern.
For the DotScan system, the system integrators at in-situ have developed custom lamps with a large field of illumination of 150 x 75 mm. High power LEDs produce blue light by using a narrow band filter. "The advantage of blue light is that it has a short wavelength, so there is less reflection and that is better for analyzing the raised dots," explains Managing Director Rainer Obergrussberger.
After embossing the Braille dots, the box is assembled and pasted. It is then folded flat and positioned on a drawer in the unit. The compact USB camera points at the flat box from above. With a resolution of 1.3 megapixels, the UI-1540SE-M model offers the ideal ratio of accuracy to data volume. The uEye captures 25 frames per second at full resolution, which allows for fast inspection. The scene to be captured has a very high dynamic range, however. The shading has to be clearly discernible without overexposure in reflecting areas. Things are made even more difficult by the fact that the Braille dots are sometimes embossed on a black background, which is a major challenge in image acquisition. For this reason, the camera takes a series of images with different exposure times and superimposes them to determine the required dynamic range.
The main challenge in developing the system was programming the algorithm. The shape-from-shading process was very slow at first and unsuitable for industrial use. After a long development phase, the developers succeeded in significantly improving the process: The image analysis, which initially took 10-20 seconds per image, can now compute up to 20 images per second.
High speed combined with a comparatively low system price sets the DotScan solution apart from competitors: A complete Braille inspection in less than two seconds cannot be achieved using other methods, such as light stripe projection or laser triangulation. In addition, the DotScan system delivers an accuracy of +/- 0.02 mm depending on the surface properties of the folding box. The required calibration is carried out with special calibration standards.
SOURCE: IDS Imaging; www.ids-imaging.com/frontend/files/SuccessStory_DotScan.pdf
About the Author
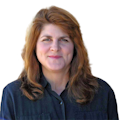
Gail Overton
Senior Editor (2004-2020)
Gail has more than 30 years of engineering, marketing, product management, and editorial experience in the photonics and optical communications industry. Before joining the staff at Laser Focus World in 2004, she held many product management and product marketing roles in the fiber-optics industry, most notably at Hughes (El Segundo, CA), GTE Labs (Waltham, MA), Corning (Corning, NY), Photon Kinetics (Beaverton, OR), and Newport Corporation (Irvine, CA). During her marketing career, Gail published articles in WDM Solutions and Sensors magazine and traveled internationally to conduct product and sales training. Gail received her BS degree in physics, with an emphasis in optics, from San Diego State University in San Diego, CA in May 1986.