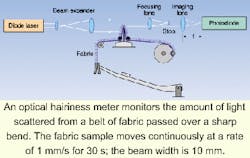
A pair of light-based instruments devised by researchers at the Ecole Nationale Supérieure des Industries Textiles de Mulhouse (Mulhouse, France) makes possible the quick and unambiguous measurement of two important textile fabric qualities: roughness and hairiness. In addition to an intrinsic roughness (related to surface topography), every fabric has an average hairiness (length and areal density of projecting fibers). Many fabrics are processed by sanding or other means to change the feel of the fabric (for example, to make nylon feel more like cotton)—processes that increase both roughness and hairiness. As in any industrial process, the ability to monitor product quality at will is all-important to maintaining consistency, thus the need for instruments that measure fabric feel to a higher precision than a swipe of the hand.
The first instrument, an optical multidirectional roughness meter, is based on the Fourier analysis of light gathered from the image of a 1-cm-long slit scanned across the cloth. A 635-nm-emitting laser diode illuminates the slit, while a beamsplitter directs the light back-scattered from the cloth to a photodiode. The researchers chose a circular scan in which the slit follows an 8-cm-diameter circle, with the slit always aimed at the circle's center. When analyzed, the signal results in a power spectrum that shows peaks corresponding to the periods of the warp, woof, and diagonal of the fabric. Power spectra taken before and after processing of the fabric exhibit decreases in peak height that give information on the amount of roughening.
The second device, an optical hairiness meter, uses the same diode laser for a light source (see figure). In the setup, a fabric sample moves in a conveyor-belt-like fashion around a sharp bend that exposes the fabric's projecting fibers to a collimated beam. The forward-scattered light is focused by a lens and zero-spatial-frequency light is eliminated by a stop. As in the roughness-measuring instrument, a power spectrum is derived from the collected signal. In this case, however, the power spectra before and after processing are integrated; their ratio gives a direct measure of the increase in fabric hairiness due to processing. The hairiness meter easily quantifies, for example, processes such as emerizing (sanding) and raising (brushing with wire-covered rollers, which produces an increase in hairiness four times greater than that produced by sanding).
The researchers note that the roughness meter is sensitive to fabric color and is thus suitable only for colorless or light-colored fabrics, while the hairiness meter is unaffected by fabric color.
About the Author
John Wallace
Senior Technical Editor (1998-2022)
John Wallace was with Laser Focus World for nearly 25 years, retiring in late June 2022. He obtained a bachelor's degree in mechanical engineering and physics at Rutgers University and a master's in optical engineering at the University of Rochester. Before becoming an editor, John worked as an engineer at RCA, Exxon, Eastman Kodak, and GCA Corporation.