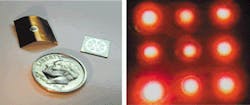
As a result of their use in laptop computers, flat-panel displays (FPDs) are made by the millions. It is only their high cost that prevents them from almost entirely displacing cathode-ray-tube displays (CRTs) for general use. The race is now on to develop a high-quality FPD that can be sold as cheaply as CRTs, with simplicity of manufacture an essential goal.
Perhaps the ultimate in ease of fabrication would be roll-to-roll processing, in which FPDs are made on a continuous sheet of flexible material and then cut into individual panels. Researchers at the University of Illinois (Urbana, IL) have developed a flexible light-emitting array based on microdischarges—a technology similar to that in plasma display panels (PDPs). Each pixel contains two electrodes, between which an electrical discharge excites a gas into emitting light. The electrodes are much simpler than those in PDPs and consist of two conducting films separated by a flexible polymer dielectric. Gas-filled holes in the polymer provide the discharge volume. The arrays can potentially be made using roll-to-roll techniques.
In one version, a polymer film 5 to 10 µm thick is spin-coated onto 25-µm-thick copper foil that serves as the cathode (a metal-coated polyimide film also serves well as a cathode). A 200-nm-thick film of nickel evaporated onto the polymer serves as the anode. An array of microdischarge cavities 50 to 150 µm in diameter is drilled through the three-layer structure either mechanically or using a Ti:sapphire laser. Finally, the structure is evacuated, backfilled with the desired gas, and sealed by lamination. A key characteristic of these microdischarge devices is that they can be filled with gas at up to atmospheric pressure and beyond.
With individually addressable pixels, the device would become an FPD; otherwise it could be used as a flexible sheet light source. The researchers have made 3 x 3 flexible microdischarge arrays in polymer film and have also fabricated a rigid version with inverted-pyramid microcavities directly onto silicon in sizes up to 10 x 10 (see figure). Replacing one of the electrodes with a screen has the effect of evening out the electric-field lines, which increases lifetime, says Gary Eden, one of the researchers. The thinness of the dielectric in the flexible device results in operating voltages as low as 90 V.
The devices have been tested for more than 100 hours with no visible or electrical sign of deterioration, although light output declines somewhat due to outgassing of the polymer. Refilling the gas brings light output to full intensity (alternatively, the use of other dielectric materials may produce less outgassing, which would reduce this problem).
Because the array operates near or above atmospheric pressure, it has capabilities previously unavailable to microdischarge devices. For example, when filled with gas combinations used in excimer lasers, the microdischarges form the same excited dimers and emit light at excimer-laser wavelengths. This light is incoherent and can be either continuous-wave or pulsed, according to Eden. The xenon iodide excimer has been tested in the University of Illinois device, he says, noting that the resulting 254-nm emission is significant because it is identical in wavelength to an emission line of the widely used mercury lamp.
A large, flexible microdischarge array could one day be used as a medical light source, Eden says. For photodynamic therapy (in which light passed through the skin into the body kills cancer cells to which chromophores are attached), a light-emitting sheet could be wrapped around a patient, providing a large dose of light in a convenient manner. Eden also sees a use for a microdischarge array as a destroyer of organic toxic gaseswhich, when passed through a nonlaminated array, would quickly be decomposed.
About the Author
John Wallace
Senior Technical Editor (1998-2022)
John Wallace was with Laser Focus World for nearly 25 years, retiring in late June 2022. He obtained a bachelor's degree in mechanical engineering and physics at Rutgers University and a master's in optical engineering at the University of Rochester. Before becoming an editor, John worked as an engineer at RCA, Exxon, Eastman Kodak, and GCA Corporation.