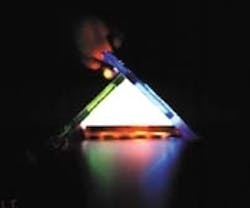
Full-color flat-panel displays made up of organic light-emitting diodes (OLEDs) share a problem with most other color displays: constructing one means fabricating a multitude of intermingled red, green, and blue pixels. In the case of OLED displays, the pixels are emitters whose colors are dependent on their chemical composition. Making a full-color OLED display in the conventional manner consists of masking off all but a third of the pixel sites at a time to create each color. Such shadow-masking introduces constraints that limit display resolution.
Researchers at the University of California, Los Angeles (UCLA), have devised a maskless technique for making full-color OLED displays. They broke from the two-dimensional world of ordinary pixel arrays and created pixels in the form of pyramids on a clear plastic diffusing substrate. In one design, the pyramids have three sides, with each side coated with a different-colored OLED. Because the vapor-phase deposition of the OLED materials is a line-of-sight process, the direction of deposition can be set so that all pyramids are simultaneously coated on the same side with the same material, leaving the other two sides untouched. Three separate depositions of different materials from directions 120° apart create red, green, and blue OLEDs on each pyramid.
In another similar geometry, the pyramids each have four surfaces. Such a geometry is useful either for four-color displays or for three-color displays that have one color dimmer than the others (in the latter case, two surfaces are coated with the same OLED material).
Triple the resolution
One property that both pyramidal geometries share is a tripling in resolution over a conventional full-color pixel arrangement. Because each pixel contains all three colors, three pyramids fit in the same space as one conventional pixel. In addition, there is no division of colors on the display surface: every point on the display is capable of emitting red, green, and blue, eliminating the usual multicolored pattern as seen from close up.
The development of the display is at an early enough stage that the researchers have not yet obtained a substrate containing a pyramidal array. To test their concept, they substituted the next-best thing: a commercially available transparent plate containing triangular ridges. Such a plate allowed them to coat an OLED material on one face of each ridge, providing an adequate test of the principle.
To try out the pyramidal concept, they built a single large pixel from an ordinary prism having three polished and two diffuse surfaces (see figure). Red, green, and blue polymer light-emitting diodes were glued to the polished surfaces. From its diffuse surfaces, the device emitted light that could be varied continuously between white and various colors.
As with any other flat-panel display, each pixel in the pyramid array must be individually electrically addressed. The UCLA researchers envisage an active-matrix scheme in which all thin-film transistors and electrical contact pads are fabricated on a glass plate, then the pyramid structures molded on top, leaving holes for the contact pads. Plastic molding is a mature technology that would not add much complication to the display's manufacture. The three different light-emitting layers could be deposited sequentially by rotating the substrate—or, with a custom setup, in a single operation. According to Yang Yang, one of the researchers, negotiations are in process with an industrial company to jointly develop the display.
About the Author
John Wallace
Senior Technical Editor (1998-2022)
John Wallace was with Laser Focus World for nearly 25 years, retiring in late June 2022. He obtained a bachelor's degree in mechanical engineering and physics at Rutgers University and a master's in optical engineering at the University of Rochester. Before becoming an editor, John worked as an engineer at RCA, Exxon, Eastman Kodak, and GCA Corporation.