OPTICAL FREQUENCY COMBS: Glass microtoroids generate combs
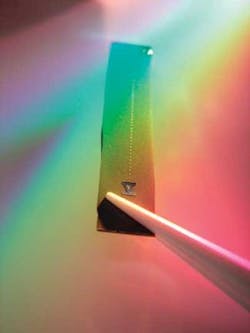
It is fitting that the next step forward for optical frequency combs should occur at the Max Planck Institute for Quantum Optics (MPQ; Garching, Germany)—the very place where Theodor Hänsch did the pioneering frequency-comb work that garnered him a piece of the 2005 Nobel Prize in Physics (see www.laserfocusworld.com/articles/294647).
Optical frequency combs have come to be widely used for metrology, in applications in which high-precision wavelength measurement is necessary. Most commonly, such frequency combs have been based on the pulse trains produced by ultrafast modelocked lasers, making for a complex and bulky setup.
Now, Pascal Del’Haye and his colleagues at the MPQ have demonstrated a simple new method to create frequency combs from micron-scale structures at heretofore unreachable repetition rates greater than 100 GHz, with an experimental precision better than 10-17.
The approach uses silicon microtoroids with a diameter of just 75 µm that are fabricated using standard semiconductor lithography techniques (see Fig. 1). The toroids act as microresonators with enormously high quality factor (the “sharpness” of their optical resonance)—on the order of 108. A continuous-wave laser at the telecommunications wavelength of 1.55 µm is coupled into a toroid via a glass nanowire, resulting in a four-wave mixing process. Two of the input photons are annihilated, producing two more photons at sideband frequencies on either side of the incident frequency, subject to energy conservation. Those newly produced sideband frequencies undergo four-wave mixing with the incident pump radiation, resulting in more sidebands. In this way, the group produced a frequency comb of some 130 lines—all without the need for the gain medium present in current approaches (see Fig. 2).1“Compared with the effort that is needed to build a modelocked laser as frequency-comb generator, it is really surprising that it is possible to generate a comb by just pumping a ring of glass with a laser,” says Del’Haye, lead author.
More power
The team compared the spectrum of the comb produced with the new approach to that produced by a conventional modelocked laser-based system (provided by Menlo Systems, a spinoff company started by MPQ to market frequency-comb systems for metrology). The group found that the comb spread over some 550 nm (approximately 70 THz) around the 1.55 µm center frequency. The lines of the comb have a comparatively large spacing, on the order of a terahertz, many times larger than that produced by the conventional modelocked laser approach. However, there is significantly more power in each spectral line of the new approach: in the milliwatt range compared to the nanowatt powers produced until now.
Those differences, says Del’Haye, make the approach ideal for some applications-the large spacing between each line could make it easier to access single lines without sacrificing precision. “This fact could prove useful for high-speed telecommunications, where one of our toroids could replace more than 100 continuous-wave lasers with channel spacing in the gigahertz range. Another conceivable application would be pulse shaping by ‘manually’ adjusting phase and amplitude of the different comb lines.”
For other applications, however, tighter spacing will be necessary, and the group is working to increase the microcavity size, which will reduce the line spacing, as well as pursuing some fundamental issues raised by the new method. “One big question is what happens in the time domain within the microcavities,” says Del’Haye. “Conventional frequency combs are generated by modelocked lasers, which generate pulses in the time domain. In our case it is not yet clear whether pulses are generated in the toroids or not (which depends on the phase relationship of the comb lines). Because of the high repetition rate of nearly one terahertz, it is tricky to measure this directly.”
Steven Cundiff of JILA (Boulder, CO), says the method is interesting. “It is quite promising, definitely the comb generation is the most compact I’ve seen. It does still require a laser, but that can be a fairly simple diode laser.” Cundiff believes further optimization will be needed to make the approach more widely applicable, suggesting that increasing the size of the resonator will be no easy task. But even as demonstrated, the approach is impressive. “The fact that the spacing is precise to better than 10-17 is the most surprising result,” he says.
REFERENCE
1. Del’Haye et. al., Nature 450, 1214 (2007).