INFRARED IMAGING: Tuning fork and polymer wire sense IR light
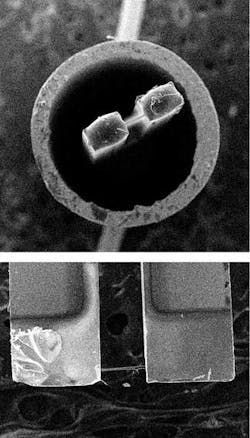
Creating the potential for lower-cost infrared sensors and arrays, researchers at Arizona State University (Tempe, AZ) have developed a thermomechanical sensor based on a 250 µm length of 1-µm-diameter polymer wire stretched taut across a microfabricated quartz tuning fork. The fork is mechanically driven at a reference frequency; when the wire absorbs radiation and heats up, its stiffness changes, altering the fork’s resonant frequency. The fork used in the experiment is commercially available for less than 10 cents.
The wire can vary in composition, but in one typical experiment it was composed of nine parts (mass) of polystyrene to one part of a polymer called SC-F105, manufactured by Seacoast Science (Carlsbad, CA). The output frequency of the fork was determined by measuring (with a transconductance amplifier) the change in output amplitude as the resonant frequency shifted from the driving frequency, which occurred at a typical rate of 0.02 normalized amplitude/Hz. The temperature sensitivity of up to 10 Hz/°C (depending on composition) and normalized noise amplitude of 1 × 10-6 indicated a temperature uncertainty due to thermal noise of 50 µ°C.
Fast response
The sensor was tested in several ways. First, it was placed in a temperature chamber and the output amplitude measured versus temperature for calibration. Next, at room temperature, laser light at a 635 nm wavelength was directed at the wire, with the wire intercepting about a nanowatt of light; the light was switched on and off every few seconds and the transient response measured. Following that, a pulsed resistive heater was placed nearby and operated at pulse widths of 20, 5, or 0.5 ms. The sensor responded to the 20 and 5 ms pulse widths; based on a calibration plot, 5 ms corresponds to 0.5 m°C.
The researchers determined the time constant of the sensor to be 50 ms, but with a caveat. “When we measured the time constant, we used a laser along with a slit to block the laser beam from hitting the quartz prongs of the tuning fork,” says Nongjian Tao, one of the researchers. “In other words, we allowed the polymer wire to be heated up rather than the prongs of the sensor. We have noticed that if the quartz prongs were heated, it takes a significantly longer time for the sensor to recover.”
The sensors could easily be combined into arrays for imaging. Potential applications of the technology include chemical sensors based on infrared spectroscopy, as well as infrared detection and imaging devices, notes Tao. The researchers have coated the polymer wires with materials such as carbon black, resulting in enhanced detection sensitivity, and are investigating other changes. “Commercially available tuning forks cost only a few cents each and are good enough for many applications,” says Tao. “However, to fully reach the potential of the tuning-fork-based infrared sensors, custom-made tuning forks are preferred.”
The group is also investigating polymer wires with better thermoresponsive properties, and is putting together a portable device around this technology.
REFERENCE
1. F. Tsow and N. Tao, Applied Phys. Lett. 90, 174102 (2007).
About the Author
John Wallace
Senior Technical Editor (1998-2022)
John Wallace was with Laser Focus World for nearly 25 years, retiring in late June 2022. He obtained a bachelor's degree in mechanical engineering and physics at Rutgers University and a master's in optical engineering at the University of Rochester. Before becoming an editor, John worked as an engineer at RCA, Exxon, Eastman Kodak, and GCA Corporation.