To perform its intended function, a microelectromechanical system (MEMS) needs its own power source. To date, magnetic-field-induced power and voltage supplies, rechargeable lithium microbatteries, miniature fuel cells, and even silicon photovoltaic (PV) sources have been used. Among these methods, solar cells offer an excellent size-to-power-density ratio compared to other power sources, are self-contained, and are amenable to on-chip integration with other MEMS circuits.
Recognizing that organic solar cells offer certain advantages over silicon solar cells, including mechanical flexibility and fabrication on a variety of substrates via spin-coating, spraying, or inkjet printing, researchers at the University of South Florida (Tampa, FL) are the first to use an organic solar cell to power a tiny MEMS device–a solar cell that has the potential to be as small as 0.01 mm2.1
Additional advantages of organic solar cells over silicon-based devices include easy isolation of the organic cell from the MEMS device, considering that the organic cell can be fabricated on any substrate, including plastic. Also, organic cells have a much higher absorption coefficient than silicon and can be fabricated with active layers as thin as 100 nm.
In this demonstration, the researchers used a four-step process to build a 2.2 cm2 miniature organic solar module consisting of 20 solar cells in series (see figure). In the first step, a one-inch-square piece of indium tin oxide (ITO) was spin-coated with resist, exposed with a photomask, and then etched to create the anode pattern. Next, the photoactive layer solution, consisting of P3HT and PCBM organic materials, was then spin-coated onto the anode layer at a thickness of 200 nm. Third, a shadow mask was created acting as a pattern for the evaporation of aluminum contacts in the required pattern on top of the photoactive layer. Finally, the aluminum cathode was deposited under heavy vacuum at a thickness of 100 nm.
Fabrication of several arrays that consisted of between 9 and 18 solar cells in series, with thicknesses ranging from 202 to 232 nm, produced open-circuit voltage values between 5.2 and 7.8 V and short-circuit current values between 13 and 55 µA.
These arrays were designed to act as a power source for running a microscopic sensor for detecting chemicals and toxins. The MEMS-based sensor is built using carbon nanotubes and has been tested using ordinary DC power supplied by batteries. When fully powered and hooked into a circuit, the carbon nanotubes detect particular chemicals by measuring the electrical changes that occur when chemicals enter the tubes. So far, the device requires a 15 V power source to work, so the researchers are planning to optimize their solar array to meet this requirement. Xiaomei Jiang, who led the research, estimates that her group will be able to demonstrate this level of power with its next-generation solar array by the end of the year.
“I think these materials have a lot more potential than traditional silicon. They could be sprayed on any surface that is exposed to sunlight–a uniform, a car, a house,” said Jiang.
REFERENCE
- J. Lewis et al, J. Renewable and Sustainable Energy 1(1) 013101 (January 2009).
About the Author
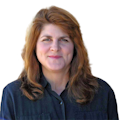
Gail Overton
Senior Editor (2004-2020)
Gail has more than 30 years of engineering, marketing, product management, and editorial experience in the photonics and optical communications industry. Before joining the staff at Laser Focus World in 2004, she held many product management and product marketing roles in the fiber-optics industry, most notably at Hughes (El Segundo, CA), GTE Labs (Waltham, MA), Corning (Corning, NY), Photon Kinetics (Beaverton, OR), and Newport Corporation (Irvine, CA). During her marketing career, Gail published articles in WDM Solutions and Sensors magazine and traveled internationally to conduct product and sales training. Gail received her BS degree in physics, with an emphasis in optics, from San Diego State University in San Diego, CA in May 1986.