OPTICAL MATERIALS: X-plate quartz enables large birefringent optics
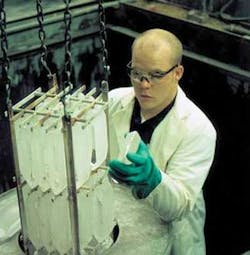
Larger quartz optical waveplates are on the way, thanks to a newly developed quartz-culturing process that grows crystals in an optimum shape. Waveplates up to 150 mm in diameter can be cut from the crystals (see figure). The process, developed at Sawyer (Eastlake, OH), is a refinement of the high-temperature and pressure hydrothermal process commonly used to produce waveplates and other quartz birefringent optics.
To achieve proper retardation, synthetic-quartz optical waveplates must be cut from as-grown quartz crystals in a specific orientation. Unfortunately, conventional synthetic-quartz crystals are thin in the dimension that corresponds to the diameter of a waveplate. The result is that synthetic-quartz waveplates are typically limited in size to 70 mm or less. The new approach produces a crystal that has its larger planes perpendicular to the crystal’s x-axis (one of the crystal’s birefringent axes; the other is y), in contrast to a conventional cultured-quartz crystal with its larger planes perpendicular to its nonbirefringent z-axis.
The process combines the use of a better “seed” (a small quartz crystal from which the much-larger final crystal is grown) with more-precise control of the environmental conditions in the steel autoclave-the 4-meter-high vessel in which the crystal is grown.
Although quartz melts at 1670°C, the hydrothermal technique makes crystal growth possible at much more manageable temperatures between 300°C and 400°C. Seed crystals are hung within the autoclave near the top; the bottom half of the vessel is filled with natural quartz, and the vessel is filled with an aqueous alkali metal hydroxide or carbonate solution. When the autoclave is properly heated and pressurized (up to 90 MPa, or 13,000 psi), a temperature difference develops between the bottom and top halves, carrying quartz in solution from the warmer dissolving chamber at the bottom to the cooler growing chamber. Growing high-quality large quartz crystals can take up to a year.
“A typical seed plate at Sawyer is a zy-cut rectangular slice of quartz crystal with dimensions about 1.5 X 100 X 300 mm along the z, x, and y axes respectively,” says Vladimir Klipov, chief research engineer at Sawyer. “Smaller or bigger dimensions in x and y directions can be used for growing different crystal shapes for different optical and electronic applications. The seed is located inside the as-grown crystal and can be observed by eye through the crystal faces.”
Seeding future generations
Optical components require that the portion containing the seed crystal be cut off, says Klipov. The highest quality selected as-grown quartz crystals are used for seeds for further reproducing. “We cut them with either a diamond saw, slurry saw, or wire saw and regrow selected seed crystals again and again,” he notes.
The x-plate process requires ingredients with an order-of-magnitude higher purity, including chemicals, water, raw materials, and so on, says Klipov. Precise temperature control inside the autoclave and uninterrupted high-quality electrical power for durations longer than a year are also required. “The autoclave, with all its parts and components, should be reliable without question and tested scrupulously before the run starts,” he adds.
The resulting large waveplates, optical rotators, and polarizers can be used for a variety of laser-grade applications encompassing instrumentation, telecommunications, and defense. Even slicing the large waveplates into smaller sizes can be more economical than growing smaller waveplates using conventional processes.
About the Author
John Wallace
Senior Technical Editor (1998-2022)
John Wallace was with Laser Focus World for nearly 25 years, retiring in late June 2022. He obtained a bachelor's degree in mechanical engineering and physics at Rutgers University and a master's in optical engineering at the University of Rochester. Before becoming an editor, John worked as an engineer at RCA, Exxon, Eastman Kodak, and GCA Corporation.