Harvard researchers develop a framework for reconfigurable metamaterials
Researchers from the Harvard John A. Paulson School of Engineering and Applied Sciences (SEAS) and the Wyss Institute of Biologically Inspired Engineering at Harvard University (Cambridge, MA) have developed a general framework to design reconfigurable metamaterials. The design strategy is scale independent, meaning it can be applied to everything from meter-scale architectures to reconfigurable nanoscale systems such as photonic crystals, waveguides, and metamaterials to guide heat.
RELATED ARTICLE: Will transformation optics be the next optical revolution?
Metamaterials--materials whose function is determined by structure, not composition--have been designed to bend light and sound, transform from soft to stiff, and even dampen seismic waves from earthquakes. But each of these functions requires a unique mechanical structure, making these materials great for specific tasks, but difficult to implement broadly.
But what if a material could contain within its structure, multiple functions and easily and autonomously switch between them? As described in Nature, Katia Bertoldi, John L. Loeb Associate Professor of the Natural Sciences at SEAS and senior author of the paper, and former graduate student Johannes Overvelde, who is the first author of the paper, collaborated with Chuck Hoberman of the Harvard Graduate School of Design (GSD) and associate faculty at the Wyss, and James Weaver, a senior research scientist at the Wyss, to design the metamaterial.
The research began in 2014, when Hoberman showed Bertoldi his original designs for a family of foldable structures, including a prototype of an extruded cube. "We were amazed by how easily it could fold and change shape," said Bertoldi. "We realized that these simple geometries could be used as building blocks to form a new class of reconfigurable metamaterials but it took us a long time to identify a robust design strategy to achieve this."
The interdisciplinary team realized that assemblies of polyhedra can be used as a template to design extruded reconfigurable thin-walled structures, dramatically simplifying the design process.
"By combining design and computational modeling, we were able to identify a wide range of different rearrangements and create a blueprint or DNA for building these materials in the future," said Overvelde, now scientific group leader of the Soft Robotic Matter group at FOM Institute AMOLF in the Netherlands.
The same computational models can also be used to quantify all the different ways in which the material could bend and how that affected effective material properties like stiffness. This way they could quickly scan close to a million different designs, and select those with the preferred response.
Once a specific design was selected, the team constructed working prototypes of each 3D metamaterial both using laser-cut cardboard and double-sided tape, and multimaterial 3D printing. Like origami, the resulting structure can be folded along their edges to change shape.
This formalized design framework could be useful for structural and aerospace engineers, material scientists, physicists, robotic engineers, biomedical engineers, designers and architects. "This framework is like a toolkit to build reconfigurable materials," said Hoberman. "These building blocks and design space are incredibly rich and we've only begun to explore all the things you can build with them."
This work was supported by the Materials Research Science and Engineering Center and the National Science Foundation.
SOURCE: Harvard School of Engineering and Applied Sciences; https://www.seas.harvard.edu/news/2017/01/toolkit-for-transformable-materials
About the Author
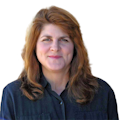
Gail Overton
Senior Editor (2004-2020)
Gail has more than 30 years of engineering, marketing, product management, and editorial experience in the photonics and optical communications industry. Before joining the staff at Laser Focus World in 2004, she held many product management and product marketing roles in the fiber-optics industry, most notably at Hughes (El Segundo, CA), GTE Labs (Waltham, MA), Corning (Corning, NY), Photon Kinetics (Beaverton, OR), and Newport Corporation (Irvine, CA). During her marketing career, Gail published articles in WDM Solutions and Sensors magazine and traveled internationally to conduct product and sales training. Gail received her BS degree in physics, with an emphasis in optics, from San Diego State University in San Diego, CA in May 1986.