Limo ramps quantity and quality of fast-axis collimation (FAC) lenses for lasers
LIMO (Dortmund, Germany), a manufacturer of high-precision microoptics for laser systems, says it has achieved a process-engineering breakthrough in the production of fast-axis collimation (FAC) lenses for all types of diode-pumped laser sources. Already used in the aerospace industry, medical technology, photovoltaics, display manufacturing, and materials processing, FAC lenses are expected to see another major increase in batch size thanks to the use of the lenses in additive manufacturing (3D printing) and lidar (light detection and ranging) systems.
Lidar systems for autonomous driving are a component that is particularly important to safety and are also used in harsh ambient atmospheres. Aside from high quality, FAC lenses also need to deliver reliable operation with long-term stability. The only way to meet these requirements is with laser systems that use high-end glass microoptics.
These FAC lenses are manufactured from high-grade glass and have an acylindrical surface. However, currently available production methods have yet to demonstrate that they can produce quantities on the order of several tens or hundreds of millions of pieces at a consistently high optical quality, and at attractive prices. But now, LIMO says it has succeeded in making the process for manufacturing FAC lenses that provide the demanded quality suitable for high-volume production.
LIMO produces its FAC lenses on wafers, which allows several thousand lenses to be fabricated from high-grade glass in a single step. When mass-producing highly complex glass optics, manufacturers face the challenge of processing large wafer areas with a consistently high level of precision. With a wafer size of 140 mm x 140 mm, the Dortmund-based manufacturer has now achieved a breakthrough to a method capable of extremely large quantities. And, according to sources within LIMO, the company already has the next, even bigger wafer generation waiting in the wings.
In the glass molding process that has typically been used up to now, glass lenses are processed at high temperatures of approximately 600-800 C. However, to produce lenses of high optical quality, the glass must be heated and cooled slowly. Considerable precision must be used in configuring the cooling process to prevent undesired stress in the material. In addition, where larger glass areas are used, temperature fluctuations occur during the heating process, and these fluctuations can only be minimized by implementing very costly process-control measures. Because of these limitations, this "hot" production method has a number of drawbacks where large quantities are involved and is not fully scalable.
The unique feature of the LIMO method is that the glass lenses are produced at room temperature. The company was able to increase the wafer size while also reducing the cycle time per wafer to under 60 minutes. The advantage of this "cold" method is that, since the glass is processed at room temperature, a higher production rate has no adverse impact on the quality of the lenses. LIMO is the world’s only manufacturer to have mastered this technique in high-volume production.
Using the cold grinding and polishing method developed by LIMO for cylindrical lens arrays, up to 20 thousand lenses can be processed simultaneously in a single step with a wafer edge length of 140 mm. The method makes it possible to freely choose from refractive acylindrical lens shapes, which can be symmetrical and asymmetrical as well as wavelike or non-periodic optical elements.
In a single grinding process, up to several millimeters must be removed from the glass surface with an accuracy of just a few nanometers. The lenses must also undergo final polishing as a last process step. The high-grade surface quality is achieved by areal polishing, which further increases the durability and stability of the glass surfaces. With its high-precision grinding process, LIMO has reached performance levels at the limit of the physically possible.
The 140 mm glass wafers are processed 24 hours a day, 7 days a week. For this to be possible, LIMO re-equipped its machinery to handle the larger format and expanded its production capacity. The company is now capable of fabricating up to 3 million FAC lenses in one year, and the goal for 2019 is to manufacture over 5 million FAC lenses. However, annual capacity is expected to increase again to over 10 million lenses until 2020. "Processing the glass wafers at room temperature makes the fabrication process very controllable, which allows us to reliably ensure high quality. We will continue to expand our capacity as needed," notes COO Dirk Bogs in summarizing the production standard achieved thus far.
SOURCE: LIMO; https://www.limo.de/en/news/press-releases/detail/news/quantity-and-quality/
About the Author
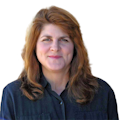
Gail Overton
Senior Editor (2004-2020)
Gail has more than 30 years of engineering, marketing, product management, and editorial experience in the photonics and optical communications industry. Before joining the staff at Laser Focus World in 2004, she held many product management and product marketing roles in the fiber-optics industry, most notably at Hughes (El Segundo, CA), GTE Labs (Waltham, MA), Corning (Corning, NY), Photon Kinetics (Beaverton, OR), and Newport Corporation (Irvine, CA). During her marketing career, Gail published articles in WDM Solutions and Sensors magazine and traveled internationally to conduct product and sales training. Gail received her BS degree in physics, with an emphasis in optics, from San Diego State University in San Diego, CA in May 1986.