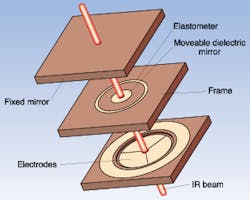
With optical networks moving toward higher and higher data rates and denser channel spacing, the probability of optical signals being lost or degraded grows greater. Engineers at Solus Micro Technologies (Westlake Village, CA) are developing a polymer-based microelectromechanical-systems (MEMS) technology in hopes of lowering the cost of tunable components for dense wavelength division multiplexing. The ability to measure the health of all channels on a fiber is becoming more and more critical in maximizing efficiency and minimizing downtime, said Terry Bailey, the company's president and chief executive officer. The drawback, however, is that optical performance monitors (OPMs) currently cost too much for sufficient deployment.
One reason, he said, is the high price of the OPM's most vital component—the tunable filter (an interferometer), which selects the desired channel for quality measurements such as power, signal-to-noise ratio, and actual wavelength. "Ideally, an OPM should be embedded in the optical amplifier at each regeneration point," said Bailey. "But the existing technologies for tunable filters are not cost-efficient enough to make OPMs affordable in the quantities needed."
Microelectromechanical-systems technology has been used to improve the performance and cost-efficiency of optical networks most successfully in optical switches and optical crossconnects. Unfortunately, said Bailey, the use of MEMS technology in tunable filters has been much less successful. "That's because traditional MEMS technology uses silicon-based materials, with extremely stiff material properties that severely limit their design space for devices," he explained.
To counter these limitations and help bring down the price of products that will incorporate tunable filter elements, Bailey's company has developed a variation of this technology that he calls compliant MEMS (CMEMS), in which components are fabricated using highly compliant elastomeric materials. The added flexibility widens the design space for devices beyond what is possible with silicon-based materials, potentially enabling development of components and assemblies that demonstrate high performance at significantly lower costs.
In one form, a CMEMS Fabry-Perot tunable filter is made of three layers, each a micromachined silicon wafer. The top layer has a high-reflectivity dielectric mirror on its inner surface and an antireflection coating on its outer surface (see figure). The second layer contains a movable high-reflectivity mirror that is the tuning element. The round mirror is suspended from a stationary perimeter by a compliant polymer layer. Electrodes on the back of the polymer layer match with electrodes formed on the third layer. The segmented electrodes enable precise adjustment of the tuning element's tip and tilt so that the two cavity mirrors remain parallel.
The properties of the polymer, which is an off-the-shelf material, are modified to fit device requirements, explained Ben Jamison, vice president of marketing and sales for Solus. The intent is to make CMEMS-based tunable components that will reduce the need for frequent signal regeneration and that will tune across the C-band (a range of 50 nm) or even the C- and L-bands combined (a range of 110 nm). "Our customers will want to put these components on a board on the network management layer," said Jamison.
The devices are in the light development stage; prototypes have been built. Testing with the first customers is slated to take place by October of this year, with volume shipping of hundreds to thousands of units to begin in the second quarter of 2002. Automated manufacturing is already in place. "We are able to do in minutes what used to take hours," noted Jamison, who added that comprehensive Telcordia trials for the devices would be a necessity.
About the Author
John Wallace
Senior Technical Editor (1998-2022)
John Wallace was with Laser Focus World for nearly 25 years, retiring in late June 2022. He obtained a bachelor's degree in mechanical engineering and physics at Rutgers University and a master's in optical engineering at the University of Rochester. Before becoming an editor, John worked as an engineer at RCA, Exxon, Eastman Kodak, and GCA Corporation.