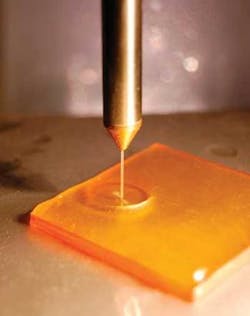
A fluid-jet optical-polishing process developed at LightMachinery (Ottawa, Ont., Canada) promises a lower-cost path to deterministic optical polishing. Traditionally, optical elements have been shaped and polished by skilled opticians; deterministic polishing automates the process and makes it more controllable and less of an art. (The magnetorheological finishing, or MRF, technique developed at the Center for Optics Manufacturing and QED Technologies, both of Rochester, NY, is the most well known example.)
Formed by former employees of GSI Lumonics, LightMachinery was awarded a contract from Lockheed Martin (Bethesda, MA) and Stanford University (Palo Alto, CA) to build a Michelson interferometer for the Helioseismic Magnetic Imager (HMI), an instrument that will fly on NASA’s Solar Dynamic Observatory spacecraft to be launched in 2008. But correcting the accumulated wavefront error produced by several optical surfaces and cement layers in the imaging optics was proving tricky. Aided by funding from the National Research Council (also in Ottawa), LightMachinery engineers approached this problem by taking a concept that had been around for a long time-fluid polishing-and making it practical (see figure).
The idea is straightforward: take a fluid that contains abrasive particles and force it in a jet onto the surface to be figured, passing the jet across the surface in an appropriate pattern. As the flow is diverted by the surface, the heaviest particles are driven outward, resulting in a donut-shaped removal area.
Dwell map
Because the donut is small (typically a 5 mm diameter, although this can be reduced to 1 mm), surface errors of relatively high spatial frequency can be polished out. Based on the shape of the starting surface, the intended shape of the target surface, and the jet-tool profile, a dwell map is calculated that determines the tool path and velocities during polishing. The process results in a surface roughness equivalent to that for conventional optical polishing.
“One of our engineers found a Ph.D. thesis written by Silvia Booij at the Delft University of Technology,” says John Hunter, president of LightMachinery. “The thesis contained a lot of basic information and convinced us that there was potential in the technology. Proprietary technology developed by LightMachinery has significantly improved the surface roughness achieved with the process as well as the speed of the process.”
Conventional optical glasses as well as fused silica can be polished using the technique; in addition, it is suitable for more-exotic materials such as crystal quartz for waveplates, IR materials including germanium and zinc selenide, and UV materials such as calcium fluoride and magnesium fluoride. Each material has a unique removal rate, and certain polishing slurries can be more optimal on certain materials.
“The spatial frequency of the correction is limited to the size of the tool and lower,” says Hunter. “One of the key benefits of the system is that is very easy to change the nozzle size and distance to the surface to minimize the tool size or to maximize the size to increase the removal rate.”
LightMachinery has developed a commercial fluid-jet polisher. Based on the initial surface shape, the target surface shape, and the fluid-jet characteristics, the tool’s software calculates and controls the polishing routine. Fluid-jet polishing of glass is already well understood; testing to optimize the technique on other materials such as semiconductors, metals, and crystals has begun.
Fluid-jet-polishing equipment is roughly half the price of MRF equipment, notes Hunter. In addition, operating costs are lower because conventional polishing slurries can be used. “The ability to match the tool size to the spatial frequency of the error of the surface is important,” he says.“Being able to quickly change the tool allows for rapid processing with a large tool and the ‘cleanup’ of higher-frequency errors with a small tool.”
While the current tool only polishes flat surfaces, a five-axis tool that will handle curved optical surfaces is under development. The five-axis system will be able to process spherical- and aspherical-radiused parts,” says Hunter. “Five axes are required to keep the tool perpendicular to the surface and at a constant distance from the surface at all times. Another key benefit of the fluid-jet polisher is the ability to process short-radius concave parts that cannot be processed using MRF technology.”
Because fluid-jet polishing is insensitive to the flex of the substrate, it is well suited to thinning semiconductor wafers to a very uniform thickness for MEMS (microelectromechanical systems) and other applications. LightMachinery is also looking at fabricating specialized surface features such as channels, and has created microchannels in silicon. Relatively wide channels are created directly with the tool, while narrower channels are fabricated by masking.
About the Author
John Wallace
Senior Technical Editor (1998-2022)
John Wallace was with Laser Focus World for nearly 25 years, retiring in late June 2022. He obtained a bachelor's degree in mechanical engineering and physics at Rutgers University and a master's in optical engineering at the University of Rochester. Before becoming an editor, John worked as an engineer at RCA, Exxon, Eastman Kodak, and GCA Corporation.