FLAT-PANEL DISPLAYS: Wavy prism sheet makes LCDs look better
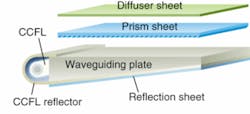
The combination of optical reflectors, refractive elements, and diffusers developed to spread illumination across backlit liquid-crystal displays (LCDs) has evolved over the years; today’s displays are bright and evenly lit, and some laptop displays are miraculously thin. There’s always room for refinement, however. Researchers at Eastman Kodak (Rochester, NY) have improved a critical component of the display optics-the microprism sheet that directs light toward the viewer-and have shown that their changes result in more light directed in the right places, as well as less aliasing between the microprism sheet and the display’s active-matrix pixels themselves.
The backlight unit commonly used in LCDs includes a cold-cathode fluorescent light, reflectors and a wave-guiding plate to distribute light evenly across the panel, and prism and diffuser sheets to angularly shape the illumination (see Fig. 1). But, particularly for cell-phone and other small displays, the grating-like structure of the prism sheet can cause aliasing (otherwise known as the Moiré effect), in which light and dark lines at a low spatial frequency mar the display’s appearance.
The Kodak researchers reduced this effect by adding a subtle waviness to the microprism pattern (see Fig. 2). While this may seem a straightforward solution, arriving at the optimum configuration involved doing Fourier transformations of the prism and pixel patterns, and then minimizing the amplitude of the Moiré component. They discovered that adding lateral waviness to the prisms wasn’t enough; the (longitudinal) phase of the waviness of each prism had to be staggered by a small, randomized amount relative to that of adjacent prisms; the result is that the prism pitch along any lateral line shows a small amount of randomization.Using computer-numerical-control micromachining, the researchers fabricated a master mold from which they made an electroformed replica, which allowed them to create 50-µm-pitch microprism sheets (with a 2 µm lateral waviness) by embossing. For test, they overlaid the resulting prism sheet on a grating having a 147 µm pitch that simulated a typical mobile-phone pixel array, and saw that indeed they had substantially reduced the aliasing.
Junwon Lee, one of the researchers, notes that the antialiasing properties of the prism sheet are especially important for small LCDs, which have pitches on the order of 150 µm; larger displays, such as those for laptop and desktop computers, typically have pitches of 250 µm or larger and suffer less aliasing in general. (Lee and his colleagues are now at Rohm and Haas Electronic Materials, also of Rochester, NY).
A manufacturable design
To optimize the sheet’s light-shaping properties, the researchers turned to optical-design software, which allowed them to vary parameters such as the radius of curvature of the prism’s backface, the height, and the tilt angles of the flat and curved sides. Manufacturability concerns forced them to also include and optimize a small flat at the prism’s apex. Because a circular cross section for the curved side (the one that directs light to the viewer via total internal reflection) is much easier to produce with diamond-machining tools, the researchers excluded the use of conic cross sections, even though they could result in higher on-axis brightness for the viewer. A test against a prism sheet taken from a conventional laptop-backlighting unit showed a peak brightness of 5553 nits for the experimental sheet, versus 4397 nits for the control sheet.
Ultimately, a roll-type mold could be made to realize roll-to-roll manufacturing of the microprism sheet, says Lee. The wavy shape would be created in the mold by a single-point diamond-turning machine with a fast-tool servo.
REFERENCE
1. J. Lee et al., Optics Express 15(14) (July 9, 2007).About the Author
John Wallace
Senior Technical Editor (1998-2022)
John Wallace was with Laser Focus World for nearly 25 years, retiring in late June 2022. He obtained a bachelor's degree in mechanical engineering and physics at Rutgers University and a master's in optical engineering at the University of Rochester. Before becoming an editor, John worked as an engineer at RCA, Exxon, Eastman Kodak, and GCA Corporation.