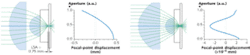
Given the choice between developing a custom optical system or one that can make do with commercial “off-the-shelf” lenses, any designer would choose the latter. Sometimes, though, when working with limited choices, it can take more than one try to really get it right.
Peter Macko and Maurice Whelan of the European Commission–DG Joint Research Centre (Ispra, Italy) needed to fabricate a holographic diffractive optical element (HDOE) via optical lithography, and decided to create their own lithographic system using commercially available lenses. Because spherical lenses are less expensive than aspherical, they restricted the design to the former, and developed a two-element optical system made of a plano-convex lens and a half-ball lens (along with a glass plate to separate the half-ball lens from the image plane).1
However, the resulting HDOE was less efficient than expected, and the researchers traced the subpar performance back to the optics used in the lithographic fabrication. So they used aspherical (but still commercially available) optics in their second design, and achieved everything they had wanted to.2
The second was almost as simple as the first, containing an aspherical plano-convex lens produced by Edmund Optics (Barrington, NJ), and a slightly smaller half-ball lens. The resulting HDOE was highly efficient.
The researchers were trying to increase the collection efficiency of fluorescence light emitted from biochip readers, which are used in biomedical diagnostics: the presence of fluorescence shows the presence of labeled target molecules captured by antibodies fixed to the chip. But most of the fluorescence is totally internally reflected in the substrate, necessitating the addition of a flat HDOE mounted on the chip to extract the light.
The HDOE is 100 µm thick (a volume hologram) and is designed to work in the 580-to-660 nm range. The parameters of the optical system to produce it were partially determined experimentally. The researchers varied the spacing between the two lenses, as well as the thickness of the glass plate, to minimize longitudinal spherical aberration (which was the problem with the original design). Each time they changed a spacing, they recorded another HDOE, then tested the efficiency of the HDOE on an actual biochip (but using a thin layer of fluorescing dye on the biochip rather than an actual biomaterial).
The improved lithographic system had a longitudinal spherical aberration reduced from the original by a factor of about a thousand (see figure). The resulting HDOEs were twice as efficient as the original HDOEs—and about seven times as efficient as having no HDOE at all on the biochip.
REFERENCES
- P. Macko and M. P. Whelan, Optics Letters 33(22) p. 2614 (Nov. 15, 2008).
- P. Macko and M. P. Whelan, Optics Letters 34(19) p. 3006 (Oct. 1, 2009).
About the Author
John Wallace
Senior Technical Editor (1998-2022)
John Wallace was with Laser Focus World for nearly 25 years, retiring in late June 2022. He obtained a bachelor's degree in mechanical engineering and physics at Rutgers University and a master's in optical engineering at the University of Rochester. Before becoming an editor, John worked as an engineer at RCA, Exxon, Eastman Kodak, and GCA Corporation.