Aluminum optics meet short-wavelength application requirements
Although aluminum optics are a strong candidate to satisfy growing demand for low-cost, lightweight optics in military and spaceborne applications, it has historically been difficult—if not impossible—to reliably generate raw aluminum surfaces with the necessary surface parameters needed for high-performance, short-wavelength (visible and ultraviolet) applications such as satellite imaging. But engineers at Coherent (formerly Tinsley of Richmond, CA) have solved these challenges with fourth-generation fabrication processes that produce aluminum aspheric mirrors (even for common 6061-T6 alloys) up to 800 mm in diameter with surface figures as good as λ/100 (at 633 nm), with root-mean-squared (RMS) surface roughness of just a few angstroms.
Rather than follow traditional means of applying a thick cladding of a harder and more easily polished metal like nickel to the aluminum substrate and suffer with thermally sensitive bimetallic optics, Coherent polishes aluminum in a multi-step process. Single-point diamond turning (SPDT) is followed by Fizeau interferometry and/or a phase-measuring microscope test to program a robotic system for "deterministic polishing." That is, variable dwell times are programmed for different locations on the optic as it is re-polished using a pad size appropriate for the optic and intended figure, together with proprietary polishing slurries. The optical surface is iteratively re-measured and subjected to more deterministic polishing as necessary, to remove the SPDT grooves, correct any figure errors, and bring the surface roughness to the target value. After heat treating to relieve any stress-induced polishing, a binding material is applied to the surface, followed by a dielectric coating to provide the target reflectivity characteristics. Reference: https://goo.gl/mLsa43.
About the Author
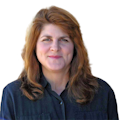
Gail Overton
Senior Editor (2004-2020)
Gail has more than 30 years of engineering, marketing, product management, and editorial experience in the photonics and optical communications industry. Before joining the staff at Laser Focus World in 2004, she held many product management and product marketing roles in the fiber-optics industry, most notably at Hughes (El Segundo, CA), GTE Labs (Waltham, MA), Corning (Corning, NY), Photon Kinetics (Beaverton, OR), and Newport Corporation (Irvine, CA). During her marketing career, Gail published articles in WDM Solutions and Sensors magazine and traveled internationally to conduct product and sales training. Gail received her BS degree in physics, with an emphasis in optics, from San Diego State University in San Diego, CA in May 1986.