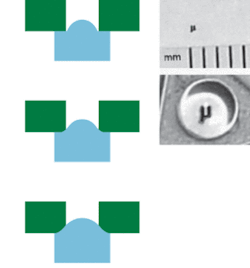
Glass molding has long been an alternative to traditional grinding and polishing for lens fabrication. For example, aspheric glass illuminator (condensor) lenses both large and small can be made economically by molding, although their transmitted-wavefront quality is low. As for precision optics, small glass lens elements can be fabricated using molds of heat-resistant materials such as carbide alloys. Such molds must be precisely machined and are expensive; molds for lens arrays require more machining steps and are even higher in cost.
Developing simpler ways to mold small glass optics could bring rewards; not only are molded glass lenses used in digital still cameras and mobile-phone cameras, but limited supplies of molded lenses have on occasion been the limiting factor in the production of these consumer devices. Other uses for molded glass optics include fiberoptic coupling and laser-diode collimation, and, for molded microlens arrays, optical interconnects and CCD cameras. High-volume production is key for all these applications.
A group at Ohio State University (Columbus, OH) is refining a glass-lens-molding process in which the mold consists simply of a hole in a piece of metal (or, in the case of a mold for a microlens array, holes). The mold is pressed into glass that is heated above its transition temperature; the glass bulges into the holes, with the shape of the glass surface determined by relaxation induced by the forming stress (see figure). If conditions are right, the bulge of glass takes a spherical shape.
The researchers investigated the use of large-diameter (3 to 4 mm) and small-diameter (less than 1 mm) holes, as well as chamfered versus sharp corners. In an initial test, a 6.53-mm-diameter block of BK7 optical glass or soda-lime glass was heated-to a taffylike consistency, according to Allen Li, one of the researchers-and pressed between the mold and a flat piece of metal. At first the glass bulged into the desired spherical shape; when more pressure was applied, the glass began to extrude into the hole, contacting the sides of the mold and undesirably distorting the lens.
Ten lenses of soda-lime glass were formed at 680°C and 570 kPa by a 3.58-mm-diameter hole, annealed, and their surface shapes measured by a coordinate-measuring machine with a 1-µm positional and a 2-µm measurement accuracy. Most of the data points of the individual lenses varied from the fitted curve shape for the average of the ten lenses by no more than about 2.5 µm, and the total absolute error of the lenses was less than the measurement errors.
Smaller lenses were fabricated from a Sumita low-molding-temperature glass with a glass-transition temperature of 285°C, and formed at a temperature of around 340°C. A brass substrate with 500-µm-diameter diamond-turned holes was used to create a 25-element microlens array; the only optical property of these lenses measured was their focal length, which was 8.43 mm with a standard deviation of 0.14 mm.
Smoothness and accuracy of the edges of the holes were critical, as was achieving the proper forming speed. With these early experimental results, the researchers would like to develop a firmer theoretical base for the process based on properties of the molds and glass, as well as on the molding conditions; in parallel, they will pursue numerical (finite-element) analyses. They hope in the future to mold glass lenses directly onto micro-optoelectronic devices.
REFERENCE
1. G.C. Firestone and A.Y. Li, Applied Optics 44(29) (Oct. 10, 2005).
About the Author
John Wallace
Senior Technical Editor (1998-2022)
John Wallace was with Laser Focus World for nearly 25 years, retiring in late June 2022. He obtained a bachelor's degree in mechanical engineering and physics at Rutgers University and a master's in optical engineering at the University of Rochester. Before becoming an editor, John worked as an engineer at RCA, Exxon, Eastman Kodak, and GCA Corporation.