Laser materials processing is focus of Gooch & Housego HALO project
Ilminster, England--Gooch & Housego announced the start of work on the HALO (High power Adaptable Laser beams for materials processing) technology transfer project. Inaugurated in September and funded as part of the EU FP7 program, the project will develop and apply research into materials processing to improve both efficiency and capability in this area, says Matthew Peach in an article on optics.org.
The HALO project will look at how both continuous-wave (CW) and pulsed laser systems can improve efficiencies in welding, cutting sheet metal and glass (with thickness ranging from < 1 mm to 25 mm), and applying the necessary elements to enable significant advances in lasers for materials processing.
Optics.org interviewed Andrew Robertson, Gooch & Housego's senior VP, business technology & development, who is coordinating the HALO R&D project. Robertson said, "In the HALO project G&H is the coordinator and we are leading a couple of the work programmes. The premise of the project is that different types of laser beam can do different jobs better, such as cutting and processing materials, whether the laser beam profiles are annular, Gaussian or top hat. A laser that can adapt its beam dependent on application is a more useful tool than one that cannot." Robertson continues, "With ORC in Southampton, we are developing a new type of fiber laser and at our Torquay facility we are developing novel fused fiber components. For example, we plan to use photonic crystal fibers to develop components for pump beam conditioning and beam re-shaping. Such components should allow the laser beam to be adapted with minimal change to the laser cavity, enabling different types of beams to be emitted."
G&H will also be developing components for adjustable beam diode-pumped solid-state (DPSS) lasers and will be working closely with Trumpf on this task.
Robertson added, "G&H specializes in the development and manufacture of high power, free-space components at our Ilminster [Somerset, UK] facility; critical in these systems will be the development of Q-switches that create energetic pulses for the adaptable beam lasers as well as components that will enable the switching between different beam shapes.
The consortium will be investigating the cutting of brittle materials such as glass as well as sheet metals. This is a €5.7m project," Roberston said. "The industrial partners are working with a matched funding model, so they put in some R&D funding with is matched by EU. Markets of interest are micro and macro machining. It could also be aimed at biomedical applications or any other application where lasers are used. But the overall aim is to maintain the leading competitive position of European manufacturing."
SOURCE: optics.org; http://optics.org/news/3/12/32
About the Author
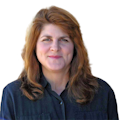
Gail Overton
Senior Editor (2004-2020)
Gail has more than 30 years of engineering, marketing, product management, and editorial experience in the photonics and optical communications industry. Before joining the staff at Laser Focus World in 2004, she held many product management and product marketing roles in the fiber-optics industry, most notably at Hughes (El Segundo, CA), GTE Labs (Waltham, MA), Corning (Corning, NY), Photon Kinetics (Beaverton, OR), and Newport Corporation (Irvine, CA). During her marketing career, Gail published articles in WDM Solutions and Sensors magazine and traveled internationally to conduct product and sales training. Gail received her BS degree in physics, with an emphasis in optics, from San Diego State University in San Diego, CA in May 1986.