VISIBLE ILLUMINATION: Mini white-light source has tunable color temperature
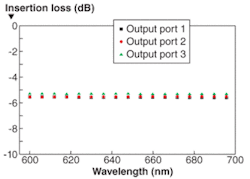
The synthesis of uniform white light from separate red, blue, and green LEDs gets more difficult as the area to be illuminated gets smaller and more akin to the size of the LEDs themselves. Options that rely on diffusers face a tradeoff: the more heavily diffused the light is (and thus the more evenly mixed), the more of it gets lost. Researchers at the Fraunhofer Institute for Applied Optics and Precision Engineering (Jena, Germany), LG Electronics (Gumi-City, Korea), and YonSei University (Seoul, Korea) have come up with a low-loss approach that in addition produces multiple outputs with precisely matched color and optical power.1
The layout is superficially simple: three optical fibers, each attached to an LED of a different color, are fused and twisted together for a short length to mix the colors, then separated again to form three high-quality white-light sources (a “3 × 3” configuration). The details are complex, however. In fact, the researchers rely on a precise theoretical model, which shows that twisting and tapering creates a change in the refractive index. If the fibers are twisted correctly, the fused portion has an effective refractive index that varies quadratically with the distance from the center at the proper rate to achieve optimum mixing.
The researchers used hard-polymer-clad (HPC) fiber with a 200-µm-diameter pure silica core and a 15-µm-thick low-index polymer cladding. The fibers were tapered to an elongation length of 15.5 mm and a waist of 130 µm, forming a unit only 0.3 × 1 × 15 mm in size. The fibers, which had a numerical aperture of 0.38, were butt-coupled to the red (635 nm), green (529.9 nm), and blue (442.7 nm) LEDs and were laser spot-welded to ceramic ferrules attached to the LEDs. Transmission testing done with light from a tungsten-halogen lamp showed an insertion loss of about 5.5 dB and an excess loss of 0.8 dB for each of the three fibers (see figure).
One of the researchers’ aims was to create a multiple-output source that emitted white light tunable over a range of color temperatures. To achieve this, the power level of each of the LEDs was controlled independently by an eight-bit digital-to-analog converter, allowing the color temperature to be precisely adjusted to the white-light standards D50 (5000 K), D55 (5500 K), D65 (6500 K), and D75 (7500 K), as well as all color temperatures in between.
Matched luminance
The color coordinates of all three fiber outputs matched each other precisely, with all three sitting at the same point in the pure-white zone on the CIE chromaticity diagram. More remarkable than this, though, was the similarity in luminance for the three fiber outputs: fiber ports 1, 2, and 3 exhibited luminances of 10078 cd/m2, 10094 cd/m2, and 10062 cd/m2, respectively–a standard deviation of 13.06, or only 0.13% of the average of the luminance values. The device was tested as a multiple illuminator for a 0.44 in. backlighting unit (BLU), with good results.
Yonsei University scientist Kyunghwan Oh notes that, in addition to use in small BLUs, the 3 × 3 visible-light multiplexer has potential for medical use (for example, illumination for endoscopic surgery that requires multiple ports) and for microbiological experiments such as research into photosynthesis, which can require multiple luminance-matched sources. The researchers are working on larger multiplexer sizes: 5 × 5 and 7 × 7 for HPC fiber, and more than 10 output ports for all-plastic optical fiber.
REFERENCE
- J.K. Kim et al., Optics Express 16(22) 17319 (Oct. 27, 2008).
About the Author
John Wallace
Senior Technical Editor (1998-2022)
John Wallace was with Laser Focus World for nearly 25 years, retiring in late June 2022. He obtained a bachelor's degree in mechanical engineering and physics at Rutgers University and a master's in optical engineering at the University of Rochester. Before becoming an editor, John worked as an engineer at RCA, Exxon, Eastman Kodak, and GCA Corporation.