LIGHT-EMITTING DIODES: ZnO does away with green-LED problem
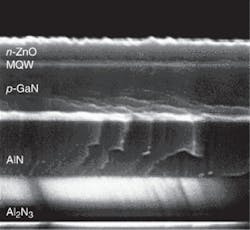
While blue and red LEDs can be made to shine brilliantly and have a long life, high-brightness green LEDs tend to die early. Now, scientists at Northwestern University (Evanston, IL) and Nanovation SARL (Orsay, France) have developed a type of green LED that has the potential to burn brightly while enduring year after year. Still in the early prototype stage, the LED has a different makeup that keeps the indium within its diode structure from diffusing over time and reducing the diode’s light output.1
The prime mover for the research is solid-state lighting. One of the most efficient forms of LED lighting is based on a combination of ultrabright blue, green, and red LEDs, which, in the right proportions, can produce white light without the use of phosphors. Both blue and green LEDs are based on an indium gallium nitride (InGaN) diode structure; increasing the amount of In within the active layers shifts the output toward longer wavelengths, making green emission practical.
However, if the indium content is high enough the InGaN layer becomes unstable at elevated temperatures, causing the LED to dim or burn out. Although such temperatures are much higher than a green LED would ever experience in operation, the LED fabrication process itself reaches these temperatures. Thus, high-brightness green LEDs begin their existence with a built-in handicap.
Zinc oxide on top
The problem is the p-GaN layer, which is the last layer grown; because it has the highest fabrication temperature of all the layers, its deposition destabilizes the InGaN light-emitting layer below. So the researchers did two things. First, they flipped the LED’s structure so that the p-GaN layer was on the bottom and thus the first to be fabricated. Second, they replaced the conventional n-GaN layer, which would have ended up on top and had the same high-temperature problem, with another semiconductor—zinc oxide (ZnO).
With a small lattice mismatch of 1.8% and the same structure as GaN, ZnO integrates well with nitride devices, and in addition can be fabricated at temperatures that don’t degrade InGaN. While ZnO had previously been combined with GaN to create ultraviolet emitters, this is the first time it has been used with InGaN to create a green-emitting hybrid LED. An additional benefit of the ZnO is that its refractive index of 2.0 is lower than the 2.5 refractive index for GaN, a change that improves light-extraction efficiency.
The fabricated hybrid LED has a turn-on voltage of 2.5 V and emits at a wavelength of 510 nm at a 400 µA current, shifting to 504 nm at a current of 1000 µA. Because it is a first prototype, the LED is not very bright or efficient, but further development will result in more-efficient versions.
The performance of this type of LED is limited by the quality of the p-GaN on which the active layer is grown, notes Manijeh Razeghi, one of the Northwestern researchers. By growing the LEDs on high-quality AlN/sapphire templates and using a doping technique developed by the researchers, the p-GaN quality can be significantly improved.2 “Conventional dislocation-reduction techniques such as lateral-epitaxial-overgrowth, hydride vapor phase-epitaxy templates, or the use of free-standing GaN substrates are also compatible with our approach,” says Razeghi. “Thus it is expected that, with optimization, the efficiency will exceed that of conventional InGaN green LEDs.”
Near-term improvements will include the optimization of electron and hole current spreading by adjusting n-ZnO and p-GaN thicknesses, notes Razeghi. The etch depth of p-GaN is also under investigation to allow more-uniform injection of holes. “Thicker green active layers are also being developed,” she adds. “As ZnO regrowth temperature (unlike GaN) is lower than that of InGaN-based multiple quantum wells (MQWs), thicker InGaN layers will be more stable and should lead to higher LED output powers.”
As for longer-term research, the researchers are working on the development of reliable p-ZnO, which would allow them to place the p layer on top, eliminating the requirement for an inverted structure.3
REFERENCES
- C. Bayram et al., Appl. Phys. Lett. 93, 081111 (2008).
- C. Bayram et al., Appl. Phys. Lett. 92, 241103 (2008).
- www.nanovation.com
About the Author
John Wallace
Senior Technical Editor (1998-2022)
John Wallace was with Laser Focus World for nearly 25 years, retiring in late June 2022. He obtained a bachelor's degree in mechanical engineering and physics at Rutgers University and a master's in optical engineering at the University of Rochester. Before becoming an editor, John worked as an engineer at RCA, Exxon, Eastman Kodak, and GCA Corporation.