Collaboration and competition breed industrial-laser success
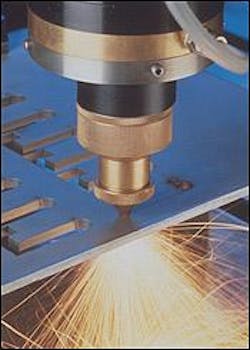
With a strong machine-tool and manufacturing history, it is no wonder that the European Union has become a major player in the laser materials-processing market. In fact, for more than a decade, the European Union has been not only a competitor in this market but a dominating force worldwide, both commercially and technically.
A look at the numbers tells the story (see Fig. 1). In 1999, Western Europe accounted for 36%, or $1.28 billion of the $3.6 billion world market for laser materials processing, according to Arnold Mayer of Op-Tech Consulting (Taegerwilen, Switzerland). In 2000, Western Europe's share dropped to 32%, or $1.46 billion, of the $4.6 billion world market. (According to Mayer, the decrease was primarily due to a 15.5% increase in the average Euro/USD exchange rate.) In 2001, Western Europe's share rose again to 35%, or $1.35 billion, of the $4.2 billion world market.What accounts for such consistent performance? A combination of factors, including government investment, competitive drive, a long history of machine-tool excellence, and good timing. Since the mid-1980s, federal and state agencies across Europe have poured billions of dollars into building a technology- and application-development infrastructure that leverages industry and academic expertise in a cooperative environment that will ensure E.U. manufacturers remain competitive in the global marketplace.
Initially, much of this funding and support was provided through E.U.-sponsored projects such as Eurolaser, sponsored by the Eureka program, which was established in 1985. Begun in 1986 and ending in 1998, the Eurolaser project, "Evaluation and Development of Industrial Lasers for Material Processing," attracted millions of dollars and dozens of other resources from government, academia, and industry throughout Europe to develop laser-based products and applications that would ensure small businesses throughout the E.U. could be competitive on the world market. Over its 12-year run, Eurolaser projects focused on high-power carbon dioxide (CO2), excimer, and solid-state lasers; other types of laser systems for industrial and medical applications; and improving efficiency, reliability, cost, and technical aspects of these products. Participants included vendors and state agencies from Germany, Hungary, Greece, Norway, Spain, Denmark, Belgium, the United Kingdom, Austria, Italy, Russia, Slovenia, and Ireland.
More recently, Eureka launched Eulasnet, an umbrella project intended to facilitate R&D and technology transfer involving lasers in processing industries. This three-phase collaborative effort, which is slated to run through December 2005, again brings together industry, research institutions, and universities from 17 E.U. members, with emphasis on developing new technologies and applications for materials processing in a number of industries. Potential application-development areas are expected to include hybrid processes, photo-assisted microreactions of polymers, laser bending of large-scale components, and microprocessing with subwavelength resolution.
Eureka programs are funded by the individual governments but not by the European Union, which has its own market- and technology-development initiatives. Over the last decade, industrial-specific E.U.-funded programs have included ESPRIT (European Strategic Programme for Research and Development in Information Technology) and the Industrial and Materials Technologies (IMT) program (also known as Brite-Euram 3), the second largest of 15 programs under the E.U. Fourth Framework. Total budget for the IMT program from 1994 to 1999 was €1.7 billion (US$1.54 billion). The technical scope of the program included production technologies, aeronautics, and surface transport means, all of which covered some aspect of laser-based materials processing.
"Europe has a very strong machine-tool industry, and the guys in that industry had the right idea with what to do with lasers," said Peter Wirth, president, CEO, and chairman of Rofin-Sinar (Hamburg, Germany). "We have been lobbying here, especially in Germany, with our government institutions in R&D, not for laser or source development but for the applications."
As a result, Europe is now "a little further ahead than the rest of the world with respect to integrating laser technology into manufacturing," according to Reinhart Poprawe, director of the Fraunhofer Institute for Laser Technology (ILT; Aachen, Germany).
The market leader
If Europe is slightly ahead in industrial-laser adoption, Germany is by far the market leader within the E.U., in terms of both production and consumption. For more than a decade, Germany has accounted for about 40% of the world market for industrial lasers used in materials processing (see Fig. 2). Not only is Germany home to the two leading suppliers of these products—Trumpf and Rofin-Sinar—but utilization of this technology in German manufacturing is prevalent across a broad spectrum of businesses, from small job shops and jewelry makers to the auto, aerospace, and ship-building industries.According to the Working Group on Lasers for Materials Processing of the VDMA (Association of German Machinery and Systems Manufacturers, or Verband deutscher Maschinen und Anlagenbau; Berlin), the total number of lasers manufactured in Germany grew by more than 150% between 1994 and 1998, while the total number of laser systems manufactured and laser-system exports rose more than 190% during that same period. This growth continued into 2001, with sales of industrial CO2 and Nd:YAG lasers up 17% and orders up 11% in the first half of 2001, according to the VDMA. While exports of German industrial lasers were down in 2001, domestic sales were up.
"We have a very traditional fine and ultrafine mechanical industry in Germany, and it is absolutely necessary to supply high-quality components for lasers and optics to the job floor," Poprawe said.
In addition to ongoing investment at the state and federal levels, the German industrial-laser business has benefited greatly from the country's well-established network of R&D institutes and educational programs geared toward the engineering community and end users. According to Poprawe, Germany is home to more than 20 institutes and research organizations dedicated to lasers, including Fraunhofer (which has three laser-specific facilities in Germany and research centers worldwide), the Institute for Machine Tools and Industrial Science at the Technical University (Munich), the Bavarian Laser Center (Erlangen), and the Faculty for Production Engineering at the University of Erlangen-Nürnberg.
Not only do these institutes work closely with industry partners to develop new technologies and applications, but they have spawned a number of commercial ventures on their own. Fraunhofer is marketing a range of industrial diode laser systems based on applications research conducted during the 1990s, and in the past year alone the institute has launched three laser-specific start-ups. One of these is EdgeWave (Aachen), which is commercializing high-power solid-state slab-laser technology developed at Fraunhofer for use in very precise high-speed cutting applications.
This collaborative approach has also created a manufacturing base in Germany that is very well educated in laser technologies and their applications, which has in turn led to the development of many new applications (see "Germany sets sights on educating U.S. customers," p. 162). Cutting and welding remain the dominant industrial-laser applications, thanks in large part to the German auto industry, which has played a significant role in boosting the country's industrial-laser business (see photo). But according to the VDMA German manufacturers are also using CO2, Nd:YAG, and diode lasers to:
- cut and weld pacemakers, batteries, hydraulic components, and other miniaturized precision components;
- mark and process nonmetals, such as acrylic material in advertising, ceramic substrates in electronics, industrial textiles, wood, paper, and printed circuits (see Fig. 3);
- microprocess resistors for hybrid and SMD circuits, integrated circuits, and control and converter circuits for automotive, medical equipment, and household appliances;
- weld, solder, harden, or remelt thin-walled plastics and metal foils in the packing industry and polymer-coated printing plates for information-technology applications.
Other investment
Germany is by no means alone in its broad-based support of industrial-laser technologies and applications. Laser-based material processing is also firmly entrenched throughout Italy, France, the United Kingdom, Switzerland, The Netherlands, and northern Europe.
Italy is second only to Germany among European providers of industrial-laser systems and applications. Work on CO2 laser sources for industrial use began earlier in Italy than in other European countries. In 1976, an agreement between CISE (Milan) and Valfivre (Florence) produced slow-flow CO2 sources with power up to 500 W that were sold by Valfivre. The first laser cutting systems, developed from punch-press frames, were displayed at Milan's EMO in 1979. In 1980, the National Research Council (NRC) launched a special project, "High Power Lasers," to promote laser-application centers at Fiat Research Centre (Torino), RTM (Vico Canavese), CISE, and Centro Laser (Bari) and to develop high-power CO2 laser sources at CISE. However, the NRC project ended in 1982 following a lack of involvement and support by industry, academia, and public R&D centers.
Today, sheet-metal cutting and laser marking are Italy's top industrial applications. More than 1500 laser centers are operating in Italy, with many shops running six or more systems, primarily for cutting. Italian manufacturers have also developed advanced industrial solutions in pipe welding, ship-structure welding, and gold welding; laser robots; three-dimensional cutting of tubular structures; and jewelry welding.
In France the main participants in industrial laser processing are all members of the Club Laser de Puissance (CLP), a nonprofit association developed to promote laser materials processing and industrial applications. The backbone of the CLP is the R&D and technology transfer centers located throughout France, including Bourgogne Technologie (Le Creusot), Institut de Soudure (Yutz), and IREPA Lasers (Strasbourg), CLAIRE (Aix en Provence), and CLFA (Arcueil), a German-French collaboration center near Paris.
The development of industrial applications started in the 1970s with the drilling of cigarette paper using CO2 lasers and the first CO2 laser sheet-metal cutting machines. Today the French market for laser sheet-metal cutters is dominated by European manufacturers: Trumpf, Bystronic, Rofin-Sinar, Balliu, LVD, and Prima, with some Japanese imports from Mazak and Amada. The laser-based metal-cutting field has experience strong growth during the last decade, with more than 100 machines sold each year. The number of installed lasers with powers of >500 W is near 1000 units. Of these, 85% are used for cutting and 15% for welding applications. Marking has also become a high-growth market. In addition, high-power diodes are making inroads into the industrial sector through efforts by Rofin-Sinar (Hamburg), Lasersource (Saint-Nom-la-Bretéche), and Fisba Optik (St Gallen).
In the United Kingdom, government, academia, and industry have been extremely involved in nurturing the use of lasers for materials processing for many years. Since 1967, TWI (The Welding Institute; Cambridge) has been at the forefront of laser materials processing in the U.K. The first oxygen-assisted laser cutting was performed at TWI using a 300-W pulsed CO2 laser; three years later TWI also introduced the fast axial flow laser and this was used to successfully develop laser keyhole welding. Current equipment at TWI includes both CO2 lasers (from 3 to 22 kW) and Nd:YAG lasers (from 2 to 10 kW).
TWI has been active in the development of techniques to improve the laser weldability of thicker section steels, particularly in the area of heavy fabrication and ship construction. TWI has also developed novel methods of joining plastics using CO2, Nd:YAG and diode lasers. In addition, TWI has been instrumental in the "Make It With Lasers" program, a long-term effort designed to help industry increase productivity, reduce costs, and improve quality by using lasers within the manufacturing process. The program, which is managed by TWI, offers workshops targeted at certain industries or the application of specific technologies.
British manufacturers have also been active in promoting this technology and its application through the Association of Industrial Laser Users (AILU), founded in November 1995 to serve the needs and interests of the growing industrial laser community and to help users make the most of laser technology. Its members include laser job shops, manufacturers using lasers, industrial R&D laboratories, and laser product and service providers. The AILU has also been instrumental in establishing the European Laser Applications Network (ELAN), a new organization intended for the promotion of laser technology in industrial sectors in Europe by cooperative actions, and to serve as the first point of contact for international inquiries.
In addition to these and other government- and industry-sponsored activities, industrial-laser R&D efforts are ongoing at most U.K. universities, including Coventry, Glasgow, Heriot-Watt, Hull, Liverpool, Loughborough, Strathclyde, Sussex, and the University of Warwick.
The next generation
As the industry matures, European laser makers and R&D groups are hard at work on the next generation of industrial products and applications that take advantage of their broad base of experience. Many of these involve new laser sources and integrated technologies that make it possible to process materials that previously could not tolerate "conventional" laser energies (see "Femtosecond lasers enhance deep drilling of metals," p. 165). At Fraunhofer, for instance, current projects include polymer welding using direct diode lasers, cleaning and polishing applications using ultrafast lasers and short-pulse lasers, and laser-induced breakdown spectroscopy.
"There is now a huge 'photonics sea' in which we can find and develop new laser technologies and applications," Poprawe said. "At the same time, there is a whole set of parameters that can and must be tailored to correspond to the application. The toolbox of lasers and laser modifications we can apply gets increasingly well-suited to the markets and applications, so matching them gets easier to do."
REFERENCES
1. O. Freneaux, Industrial Laser Solutions 15(2) (February 2000).
2. B. Marx, Laser Focus World 33(6) S5 (June 1997).
3. A. Vendramini, Industrial Laser Solutions 14(1) (January 2000).
About the Author
Kathy Kincade
Contributing Editor
Kathy Kincade is the founding editor of BioOptics World and a veteran reporter on optical technologies for biomedicine. She also served as the editor-in-chief of DrBicuspid.com, a web portal for dental professionals.