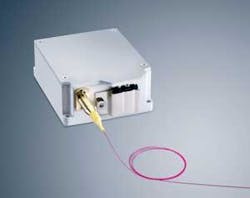
This year’s show floor at SPIE’s Photonics West (February 24 to 29; San Jose, CA) offered high-power lasers galore. Here is a brief sampling of the type of laser often in evidence–many of which trended toward being more reliable, higher in brightness, and easier to use.
Remote welding made easy
In one example, Coherent introduced a rack-mountable fiber-coupled diode laser, the HighLight 1000F, that emits 1 kW at a numerical aperture (NA) of 0.2 from a 600 µm fiber, allowing the laser system to be placed up to 50 m from the application. The 975 nm laser has closed-loop cooling; house water is used only to cool the internal chiller. Its electrical-to-optical efficiency is up to 30% after fiber delivery.
The laser has three major applications: heat treating, cladding, and conduction welding, notes Stuart Woods, director of business development at Coherent UK (Ely, England). “Heat treating and cladding is used everywhere from the oil industry for making drilling parts stronger to cladding airplane turbines,” he says. “Conduction welding is typically used in welding metal sheets less than 2 mm in thickness. Conduction welding can be found in everything from white-goods manufacturing to food-can manufacturing.”
A smaller, air-cooled 400 W version of the laser is also available, which is about the size of a microwave oven. The smaller version is well suited for plastic welding, or any form of annealing where a focused heat source is needed, says Woods.
Woods says that in addition to the care that must go into creating a product that is highly reliable, easy to maintain, and costs little to run, “beam-combining a little over a 1 kW of light from our diode bars into a fiber eight times the size of a human hair” was a technical challenge.
“Direct-diode processing is certainly seen to be the lowest cost-of-ownership technology–even lower than fiber lasers,” says Woods. “For an application like welding, where high brightness is not needed, direct-diode lasers offer the ideal solution. With 30% to 40% electrical-to-optical efficiency, direct-diode lasers are well-positioned to take a larger share of the overall welding market.”
Scaled-up thin-disk power
Another high-power laser intended for industrial use is the Trumpf (Ditzingen, Germany) disk laser, in which the laser gain medium consists of one or more thin disks with mirrors behind them, allowing heat to be wicked away axially to reduce thermal-lensing effects. The company introduced a 16 kW four-disk version of its TruDisk laser at Photonics West, which doubles the power of the previous laser while maintaining its beam-parameter product at 8 mm-mrad. This laser has a wall-plug efficiency of up to 30%.
Trumpf emphasizes the broader power scalability of its thin-disk design, and has obtained a 14 kW output in the laboratory from a three-disk laser and 5 kW from a single-disk laser.1 In fact, calculations done at the University of Stuttgart (Stuttgart, Germany) indicate that, in principle, 30 kW could be obtained from a single thin disk.2
Trumpf is also working on high-power direct-diode lasers, and demonstrated a fiber-coupled laser-diode module (see figure) that emits 100 W from a 100 µm fiber into an NA of less than 0.12. The module size is 8 × 6 × 3 cm and has a stated wall-plug efficiency of up to 40%. This module will be the building block for the company’s multikilowatt TruDiode direct-diode lasers; the first to be introduced will be a 3 kW version released by June of this year.
Quantum-cascade lasers that burn
While quantum-cascade (QC) lasers are not normally thought of as high-power, the QC lasers developed by Pranalytica (Santa Monica, CA) qualify, as their power levels are many times higher than the usual hundred-milliwatt-range levels for this kind of emitter. In fact, the 2 W, 4.6 µm room-temperature QC laser that the company introduced at Photonics West can burn a hole in a business card, as demonstrated at the show by C. Kumar N. Patel, Pranalytica’s president and CEO.
The laser comes in a compact, rugged package that needs only electrical power and operates at a wall-plug efficiency of better than 13%. (At 80 K, the laser puts out at least 4 W, for a wall-plug efficiency of grater than 24%.) The package produces a well-collimated beam with a low M2 and is designed for field use. Applications include IR countermeasures, free-space optical communications, remote sensing, and trace-gas detection using photoacoustic spectroscopy. Such high powers from a mid-IR QC laser should also enable nonlinear applications such as intracavity terahertz generation.
“Our high-power results are all for QC laser chips with a high-reflectivity coating on the rear facet; that is, the power output is the usable power output for the user,” says Patel. “As power levels have increased, the reliability of high-reflectivity coatings has taken on increasing importance. Our commercial 2 W systems and laboratory demonstration of 3 W systems are all with high-reliability, high-reflectivity coatings developed by us.” An interesting aside: Patel’s history with lasers is a long one–in 1964, when he was at Bell Labs, he invented the carbon dioxide laser.
REFERENCES
- R. Brockmann et al., Proc. Photonics West 2009, p. 7193, Session 14 (January 2009).
- A. Giesen, presentation at in-house “Technologietag Scheibe,” Trumpf Laser Schramberg (April 26, 2006).
About the Author
John Wallace
Senior Technical Editor (1998-2022)
John Wallace was with Laser Focus World for nearly 25 years, retiring in late June 2022. He obtained a bachelor's degree in mechanical engineering and physics at Rutgers University and a master's in optical engineering at the University of Rochester. Before becoming an editor, John worked as an engineer at RCA, Exxon, Eastman Kodak, and GCA Corporation.