Photonic Frontiers: Rugged Battlefield Lasers: Ruggedizing high-energy lasers for the battlefield
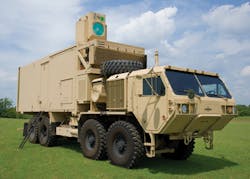
The best sign the Pentagon is serious about putting high-energy laser weapons on the battlefield is its program to ruggedize them. Development of industrial lasers has been a step in the right direction. Factories run high-energy welding lasers 24/7 for long periods and expect their lasers to operate continuously for 20,000 hours. "Our type of reliability is totally different," says Sean Ross, team lead for laser system integration technologies at the Air Force Research Laboratory (AFRL; Kirtland AFB, NM). "If we get a system out there and it fires 100 hours total, that's fine. But it has to be always ready to fire." Soldiers' lives are at stake, not corporate balance sheets.
The focus is on diode-pumped solid-state lasers powered by generators burning jet fuel. Those lasers have come a long way. "Fifteen years ago, we would have said that the number one source of unreliability was pump diodes," says Kelly Hammett, chief engineer for the directed energy directorate at AFRL. A dozen years ago, he adds, "we were saying we could never get more than 100 watts from a fiber laser." Now diode reliability is not a major issue, and multikilowatt industrial fiber lasers are standard industrial products. The challenge is keeping them working in the difficult military environment.
Military environments and laser types
Battlefields are challenging environments. Ground-based systems must contend with dust, dirt, rain, and mud, as well as vibrations when equipment is moved, which can degrade laser performance or cause damage to optics. Naval systems have to operate in high-humidity environments and withstand salt spray. Airborne systems must fit into cramped spaces and withstand vibrations. All require local power and cooling.
Diode-pumped slabs, thin disks, and fiber lasers are all in the running, but the Army picked a fiber laser for its high-energy laser mobile demonstrator (HEL-MD) shown in Figure 1. "Ruggedness is a key advantage of fiber," says David DeYoung, director of Boeing Directed Energy Systems (Albuquerque, NM), which built the HEL-MD optical system and will integrate the new laser with it. Part of the Robust Electric Laser Initiative (RELI), the system already shot down rockets, mortars, artillery and UAVs with a 10 kW industrial laser at the White Sands Missile Range in New Mexico.
In April 2014, the Army awarded Lockheed Martin (Bethesda, MD) a $25 million contract to build a 60 kW fiber laser ruggedized to withstand the HEL-MD being driven off-road. "Our laser architecture is inherently well suited" for that mission, says Rob Afzal, senior fellow at Lockheed Martin. Spectral beam combination merges different wavelengths from many fiber lasers into a single high-brightness beam.
"The individual fiber lasers are very rugged and robust," he says, because the beam stays in the fiber, avoiding contamination and vibration. Fibers deliver light to a free-space beam combiner housed in a ruggedized box, where an off-axis parabola images the array of input fibers onto a grating, which delivers a near-diffraction-limited beam through an output window and into the HEL-MD optical system. "Only in the beam combiner module do you need to keep the optics clean and the dust out," Afzal says. However, beam combination in air avoids thermal distortion that could affect power scaling in a solid.
A horse race continues among lasers because tradeoffs differ among operating environments. Specific power-watts per pound from a small package-is crucial for airborne systems. Aircraft are demanding environments, says Hammett, who worked on the airborne laser, which squeezed a megawatt-class chemical-oxygen-iodine laser (COIL) into a Boeing 747. "You got nine inches of deflection from front to back" and vibration was a constant problem in flight. Packaging is also important for the Air Force, says Ross. "In aircraft, you have lots of irregular spaces, so we want flexibility" to fit the laser into the plane.
Optical damage and measurement
"Optical damage is a huge issue," says Andy Motes, directed-energy manager at Schafer Corp.'s military aerospace office (Albuquerque, NM). Dust and dirt in the military environment magnifies risk of damage inherent with high-energy beams. Damage mechanisms include surface contamination, internal contamination of dielectric coatings, and dielectric breakdown at very high intensity. If the laser beam ignites a bit of fuzz, he says that "the carbon deposits settle and can absorb light, heating and destroying the optics." Humidity can cause delamination of optical coatings, leading to damage. Working in vacuum can avoid contamination unless vibrations break the seal. He likes fiber lasers: they reduce exposed surfaces, but says "even if you use fiber lasers, you have some free-space optics."
Designs must leave a margin below the damage threshold, but even then, Ross says they "don't expect a laser optic to last indefinitely." Over time, stresses and strains make them increasingly vulnerable. "A lot of optical damage is preceded by minor changes to appearance," he says, "so we are looking for in situ techniques to diagnose the systems before the failures occur."
Testing is essential to answer such questions as to whether laser optics have a high infant mortality and a bathtub-like failure distribution, but it's difficult. "Not too many laser optic manufacturers have 50 kilowatt lasers around for testing," says Ross. Tests using nanosecond or picosecond pulses cannot be simply extrapolated to the continuous-wave regime and larger spot sizes of laser weapons, and too few components have been tested to get good reliability statistics.
Specifying beam quality for laser weapons also poses issues. Traditionally, beam quality has been considered as a fixed characteristic, but Ross says "we're only going to run the laser for less than 10 seconds, so we look at beam quality as dynamic" because the laser needs time to reach equilibrium during a shot. Tests also will measure "power in the bucket" delivered to a vulnerable spot on the target, as shown in Fig. 2. Military planners consider that more relevant to their needs, particularly when they combine beams from multiple sources. The values of beam parameter product and m2 often used in other applications require multiple measurements and assume the ideal beam is a Gaussian, which may not be valid for high-energy lasers.Maintenance
With optical damage inevitable, high-energy lasers must be designed for field maintenance. "When you have a sealed optical system, you want to do failure-mode analysis so you have access to the parts likely to fail most often," says Hammett. The goal is to develop "line-replaceable units," so damaged modules can be quickly replaced by fresh ones. Lockheed's fiber laser design allows that because it scales power by adding modules, says Afzal. "If a fiber laser module wears out, which is going to happen sooner or later, you can imagine taking out a module and replacing it."
Portable cleanroom facilities are available, says Hammett. "We have used them on some programs. They are not ultra-clean, but they can be clean enough if you design your system to be resistant to moderate levels of cleanliness." Adapting connectors developed for fiber communications could help, says Ross. "We are looking right now into the components necessary for field-swappable fiber connections and disconnections, so you don't need a cleanroom to join two fibers together."Another possibility is designing lasers to tolerate minor faults that are repairable or unlikely to cause a critical failure. Also, developers are working on ways to speed accurate laser alignment and reduce down-time during repairs.
Cooling and power
Fielding high-energy lasers also requires ruggedizing power and cooling systems. Diesel generators are well developed for field use, but can't match the performance of the power grid. "As soon as you go to anything portable, there is the possibility for oscillatory interactions as you turn on the generator and put on a power load at the same time," says Ross. To avoid such transients, the Air Force is looking at using batteries for short-term power, then charging them with a generator.
Cooling presents bigger and bulkier problems. In one 2 kW industrial fiber laser "the thermal management system was double the size of the laser box," says Ross. Size, weight and environmental constraints mean "a conventional refrigerated air conditioning system just doesn't work" in airborne systems, Hammett says. Air Force engineers are studying two-phase evaporative cooling as an alternative, but they worry how well such systems would perform in a plane making a high-G turn.Improving efficiency can ease cooling requirements. "Everybody's fighting to get efficiency," says Motes. "At least initially we will need a low-duty cycle on the order of 10% to deal with cooling and power requirements." However, efficiency is increasing, and he hopes to reach overall electrical-to-optical efficiency of 40% in five to 10 years, easing cooling needs.
The big challenge is to take these high-energy lasers to the next level, ready to operate under harsh military conditions that pose problems different from those on the factory floor. That will take time, money, and energy. While there is no guarantee it's possible, we've already come an amazing distance.
About the Author
Jeff Hecht
Contributing Editor
Jeff Hecht is a regular contributing editor to Laser Focus World and has been covering the laser industry for 35 years. A prolific book author, Jeff's published works include “Understanding Fiber Optics,” “Understanding Lasers,” “The Laser Guidebook,” and “Beam Weapons: The Next Arms Race.” He also has written books on the histories of lasers and fiber optics, including “City of Light: The Story of Fiber Optics,” and “Beam: The Race to Make the Laser.” Find out more at jeffhecht.com.