Toothed iris diaphragm helps control radial intensity inside a femtosecond-laser filament core
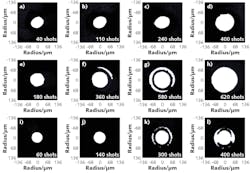
Plasma-based filamentation can occur when an intense femtosecond laser pulse propagates in optically transparent media such as air. The phenomenon has found applications in imaging, microfabrication, remote sensing, water condensation, and triggering and guiding discharges, in which the radial distribution of laser fluence inside the filament core is crucial. However, directly measuring and controlling the fluence within a filament core (which is less than 100 μm in diameter) is still a challenge due to the extremely high intensity. Researchers from the Shanghai Institute of Optics and Fine Mechanics at the Chinese Academy of Sciences (CAS; Beijing) have demonstrated new ways to directly measure and successfully control the laser fluence inside a single filament core.
In the experiments, by examining filament-fabricated microstructures on materials, the radial fluence distribution across the filament core and its evolution along the filament were spatially resolved for the first time. Instead of using a traditional circular iris diaphragm, a stellate iris was introduced to suppress iris diffraction effects. As a result, a higher laser fluence and a denser plasma inside the filament cores were generated; this was further confirmed by measuring the radial fluence inside filament cores using the filaments to drill through 15-μm-thick aluminum sheets and then looking at the resulting holes. Experimental results are in agreement with numerical simulations obtained by solving the nonlinear Schrödinger equation. In addition to understanding the filamentation process and its control, the results may also be valuable for other filament-based laser applications such as rainmaking and lightning control. Reference: H. Guo et al., Opt. Express (2020); https://doi.org/10.1364/oe.392827.
About the Author
John Wallace
Senior Technical Editor (1998-2022)
John Wallace was with Laser Focus World for nearly 25 years, retiring in late June 2022. He obtained a bachelor's degree in mechanical engineering and physics at Rutgers University and a master's in optical engineering at the University of Rochester. Before becoming an editor, John worked as an engineer at RCA, Exxon, Eastman Kodak, and GCA Corporation.