New superalloy qualified for use in Velo3D Sapphire printers
Velo3D (Campbell, CA), a metal additive manufacturing technology company, has qualified the nickel-based superalloy powder Amperprint 0233 Haynes 282 produced by Höganäs AB under license from Haynes International. This alloy, designed for high creep strength, thermal stability, weldability, and ability to be fabricated, is ideal for high-temperature structural applications like energy generation, gas turbines, and space launch vehicles to build parts like heat exchangers, combustors, nozzles, combustion liners, rocket engines, and shrouded impellers.
The first Velo3D Sapphire printer utilizing the Amperprint 0233 Haynes 282 powder will be operated by contract manufacturer and precision machining company Duncan Machine Products (DMP; Duncan, OK). The system will be the seventh in that company’s fleet of Velo3D Sapphire printers.
Powdered superalloys like this are often employed to print parts for use in high-temperature applications due to the alloy’s resistance to cracking and its ability to operate at near-melting-point temperatures. This tolerance allows parts printed with the alloy to be used in vacuum, plasma, and other demanding applications. Its high weldability makes the powder ideal for parts in larger systems because of its ability to be welded to other components. Companies engaged in commercial space activities are showing interest in laser additive manufacturing for these reasons.
How does a potential user of such alloys qualify it for laser additive manufacturing processes? I made contact with a Velo3D spokesperson and one of its customers, Chris Billings, the co-owner of Duncan Machine Products. He said, “It typically starts when a customer has an interest in processing a new alloy; for example, a demand for an additive manufacturing solution for Haynes 282. We had been having some conversations with Velo3D about this alloy and they told us they also were also hearing this from others.”
I was curious as to who puts the ‘stamp of approval’ on the laser additive manufacturing process. Billings acknowledged that the Federal Aviation Association (FAA) has something called FAA 14 CFR 21.1, which permits airframe engine and propeller manufacturers to produce additively manufactured parts certified for flight. Now, there is the Metallic Materials Properties Development Standardization (MMPDS) for additive materials, which provides guidelines about properties development and standardization. This is an industry-based source for design allowables recognized by the FAA, Department of Defense (DoD), and the National Aeronautics and Space Administration (NASA).
So, the material properties are already set by MMPDS or whoever qualified it for conventional manufacturing early on. What Velo3D and Duncan do is work together on applying a material to the laser powder-bed fusion manufacturing process. All these materials already have known chemistry and mechanical properties, along with other measurable characteristics—so after they subject samples of a material to the Velo3D laser additive manufacturing process, they then re-test the material to ensure they are still getting the same chemistry and other quality data that they started with.
The next step is to print full-sized parts from the material, then test again for performance metrics. At Duncan, they are making end-use additively manufactured parts right now that can’t be manufactured any other way.
Velo3D is one of the first additive manufacturing technology companies to offer Amperprint 0233 Haynes 282 powder to its customers. Many of Velo3D’s customers use its end-to-end solution to produce parts for use in aviation, energy, oil and gas, space, and other high-performance applications. In addition to Amperprint 0233 Haynes 282 powder, metal powders qualified to be printed with Velo3D’s technology include Hastelloy X, Inconel 718, aluminum F357, Ti 6Al-4V Grade 5, and several additional materials.
About the Author
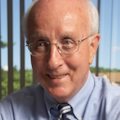
David Belforte
Contributing Editor
David Belforte (1932-2023) was an internationally recognized authority on industrial laser materials processing and had been actively involved in this technology for more than 50 years. His consulting business, Belforte Associates, served clients interested in advanced manufacturing applications. David held degrees in Chemistry and Production Technology from Northeastern University (Boston, MA). As a researcher, he conducted basic studies in material synthesis for high-temperature applications and held increasingly important positions with companies involved with high-technology materials processing. He co-founded a company that introduced several firsts in advanced welding technology and equipment. David's career in lasers started with the commercialization of the first industrial solid-state laser and a compact CO2 laser for sheet-metal cutting. For several years, he led the development of very high power CO2 lasers for welding and surface treating applications. In addition to consulting, David was the Founder and Editor-in-Chief of Industrial Laser Solutions magazine (1986-2022) and contributed to other laser publications, including Laser Focus World. He retired from Laser Focus World in late June 2022.