The age of the laser has only just begun
Two years ago, Constantin Haefner became the new director of the Fraunhofer Institute for Laser Technology (Fraunhofer ILT), Europe’s largest research center for applied laser technology. In an interview with Andreas Thoss, Haefner spoke about technological trends and his strategic response.
Andreas Thoss: If we look at current trends, digital production or the Internet of Production (IoP) stands out. How to you deal with it at Fraunhofer ILT?
Constantin Haefner: The laser is a perfect tool; its beam is massless and wear-free. At the same time, the laser allows you to observe the processes of production much more precisely. As it does so, a huge amount of data is generated. Making sense of this ‘data lake’ is one challenge in digital photonic production.
The second challenge is to comprehensively map reality into the virtual world; i.e., the design specification, the material properties, and the physics of laser-material interaction. In the past, we have mostly developed processes through human-based know-how and many trials. This is becoming more challenging in an increasingly complex and accelerated world. However, today we have more computational capabilities, simulation tools, and a deeper understanding of the underlying physics, but the real accelerator is the acquisition and networking of comprehensive and high-quality data, combined with modern machine learning and AI. Humans are liberated, and production can become more efficient, agile, and sustainable.
That’s one of the advantages of digital production: process design is assisted by machine intelligence. Digital Photonic Production enables “first time right” when going into production.
Additionally, the performance of production machines varies, even within a model, but more often due to the experience of the operator. Understanding these deviations and anticipating them by incorporating them into our process models is one of the main things we are interested in. It is about precision, repeatability, and operability. In other words, digital photonic production should allow you to use the machine the same way regardless of the environment or who operates it.
We achieve this through distributed machine learning. The data lake fed from all machines provides increased analytical and predictive capability to develop, improve, or manipulate a process. Numerical simulations build on the underlying physics and provide a guiding framework; AI loops then take those simulations and add learning from the real data, allowing for real-time data interpretation and provide recommendations to the machine control loops for how to optimize the processes. Successful operational prescriptions are then automatically rolled out to its sister machines in the cloud. The time savings are enormous.
That is why digital production is a very important topic at Fraunhofer ILT, and with the Internet of Production Cluster of Excellence—a part of the Excellence Initiative of RWTH Aachen University. And it is precisely here in Aachen that we have this structure—this data lake between the production technology institutes. We develop lasers and sensors and we develop machine learning codes and algorithms, which in turn evaluate the processes. In the end, we can optimize value chains faster and more accurately.
AT: The next big trend is additive manufacturing (AM). Your institute set a real milestone there with the EHLA technique. What’s coming up in AM?
CH: We just celebrated the 25th anniversary of the Fraunhofer ILT patent for the metal laser powder-bed fusion process, filed by three ILT scientists in 1996 (see Fig. 1). 3D laser printing was and is a big topic for us. It is also a big part of digital photonic production.
The beauty of 3D printing is certainly its design flexibility, material diversity, and lower material consumption compared to subtractive machining processes. However, when we think of a sustainable economy, we also need to consider the resource efficiency of 3D printing throughout its entire cycle, i.e. from ore to powder, from powder to product, and we are actively researching this.
Adaptive techniques during production are necessary to detect and correct defects and changes in the topology of the part. This way, we reduce scrap and achieve higher mean-time-to-failure. This pays dividends not only on first-time-right, but also on 3D printing productivity.
Predictive analysis is also part of this. You can make predictions about when and how a thing will work or fail, or what response it has. In other words, you can program the properties into the part. This opens completely new design flexibility that is only available to a very limited extent today. We also make use of this in our laser development program for aerospace platforms.
AM-specific design is still one of the biggest problems. Most engineers have learned to think in terms of ablative processes. Universities need to include the design methods of additive manufacturing early in the curriculum of design engineers to let them fully exploit and apply 3D printing capabilities.
AM is at a very interesting point now, where we have a whole range of machines in the market. We certainly must decrease costs and increase efficiency. There is still a lot of research and development work to be done, and not just in high-value engineering areas such as aerospace or medical implants.
AT: Everybody talks about climate and sustainability. How can laser technology contribute?
CH: A lot of what I said before contributes to sustainability, so does efficient 3D printing and IoP. This is really about harnessing efficiency gains. It’s not so much about completely new processes, but about working much more efficiently in process chains and thus conserving resources.
The German government is now pushing technologies that address climate change or contribute to sustainable production. Energy storage technology such as hydrogen or battery technology are major topics here at ILT. The laser plays a major role in all of these production processes.
For example, it is now a matter of bringing this hydrogen technology to the market. A research topic for us is the bipolar plates for electrolyzers or fuel cells. How can we produce them with high reliability and extreme throughput rates? Hydrogen is a very small atom that diffuses easily. Therefore, 100% tight welds are important. Once again, high precision, first-time-right, and high-quality standards—this is where the laser really shows its strength.
Our lasers for Earth observation also play an important role in climate protection. For example, we build lasers in satellites to measure winds from space very precisely and enable better weather forecasts. Gases that affect the climate, such as CO2 or methane, can also be detected from space with our lasers. It's not just about a simple laser source, but of course also about the system technology and the know-how on how to do something like this.
These are the things that drive us, and they all contribute to the sustainability we desperately need for the future.
AT: What are the key issues on Fraunhofer ILT’s bucket list for the next three years?
CH: Our team of ~600 employees at Fraunhofer ILT are committed to our core mission: contract research and technology transfer. We will continue to fulfill our mission through excellence, knowledge depth and trend scouting. On the technological side, we will systematically drive forward the development of laser processes and technology for sustainable digital photonic production, particularly in their applications in mechanical and plant engineering, energy storage, aerospace, medical technology, or mobility.
We are further strengthening our development of high-performance laser systems for production and increasingly also for space platforms. In addition, we are building new competencies for photonic solutions for quantum technology and establishing a major center for quantum science and technology in Aachen with our partners for our industrial customers. With our partner QuTech in Delft, we want to realize the first quantum Internet node in Germany (see Fig. 2).But it’s also about opening up other new areas, such as secondary sources. These are high-energy laser applications that could pay off in completely new research markets. High brilliance x-rays or particle beams can be generated by lasers and overcome the limitations of today's conventional sources. This is where lasers can break new ground.
Finally, we are seeing increasing demand for integrated solutions. This requires a high degree of systems engineering. In the context of our aerospace projects, we have established rigorous system engineering processes that we can now map to other projects. Again, it is about efficacy and efficiency: getting it right the first time.
AT: Finally, where do you see the future of the laser?
CH: The laser in the 21st century is part of an infinite number of value chains. And it is the know-how along these value chains that makes targeted use of the laser to find a win for the manufacturer or to enable processes that are otherwise unthinkable.
Certainly, the focus is increasingly shifting from the development of the beam source to the process or system technology. Here, the ILT draws on a wealth of experience to develop a tailored solution to a range of problems that arise in industry. The age of the laser has only just begun, and I am sure it will continue for a long time to come.
About the Author
Andreas Thoss
Contributing Editor, Germany
Andreas Thoss is the Managing Director of THOSS Media (Berlin) and has many years of experience in photonics-related research, publishing, marketing, and public relations. He worked with John Wiley & Sons until 2010, when he founded THOSS Media. In 2012, he founded the scientific journal Advanced Optical Technologies. His university research focused on ultrashort and ultra-intense laser pulses, and he holds several patents.
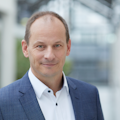
Constantin Haefner
Director, Fraunhofer Institute for Laser Technology
In November 2019, Prof. Constantin Haefner assumed responsibility as the director of the Fraunhofer Institute for Laser Technology (Fraunhofer ILT; Aachen, Germany). He also took over the chair for laser technology at nearby RWTH Aachen University. Because of fallout from the global pandemic, he had an unusual introduction as the head of these most illustrious organizations.
Haefner studied physics at the University of Konstanz and obtained a Ph.D. in laser physics from the University of Heidelberg. In 2004, he moved to the United States, first to the Nevada Terawatt Facility at the University of Nevada, Reno. Two years later, he moved to the Lawrence Livermore National Laboratory (Livermore CA) as Program Director for Advanced Photon Technologies, where he headed up the development of the world’s most powerful laser systems and conducted R&D into pioneering laser technologies until 2019.