Increasing laser welding speed for fuel cell applications
The global automotive industry is shifting to e-mobility and manufacturers are shifting from combustion engines to fuel cell engines. Their challenge is to efficiently produce fuel cells by laser welding the bipolar plates—thin plates of just hundreds of microns. Each cell contains 300 to 400 plates with a weld seam of 3 to 6 m. Suppliers find that increasing welding speed (feed rates more than 0.5 m/sec) to keep up with demand results in welding defects, leading to faulty parts and a backlog of materials.
Recent findings from the Eureka Project, based at the Fraunhofer Labs in Aachen, Germany, suggest that dynamic beam lasers may provide the automotive industry with a technological solution for economically mass-producing clean energy engines through an increased feed rate for bipolar welding.
Civan Lasers (Jerusalem, Israel), the Fraunhofer Institute for Laser Technology (Fraunhofer ILT; also in Aachen, Germany), and Smart Move (Garching, Germany) plan to solve the welding problem by implementing Civan Lasers’ dynamic beam laser technology, which can wobble the beam in megahertz frequencies, creating a faster, more accurate weld of the bipolar plates. According to Dr. Eyal Shekel, Civan’s CEO, “We are confident that the unique capabilities of the dynamic beam laser will be able to solve this challenge.”
As testing continues, it is becoming clear that dynamic beam lasers could be the game-changing solution for fuel cell engine manufacturers. Dr. Alexander Olowinsky of Fraunhofer ILT adds, “We look to reach a breakthrough in this project by using advanced sensors and complex beam shapes in high frequencies that were not available in the past.”
Civan Lasers’ dynamic beam lasers allows manufacturers to control beam shape, frequency, and sequence and to focus steering, eliminate spatter, increase welding power, and increase speed—results that open the door to countless new applications. Smart Move has created the most powerful digital state space controllers on the market, enabling customers to overcome the limits of conventional scanning solutions. Fraunhofer ILT develops new laser beam sources and components, precise laser-based metrology, testing technology, and industrial laser processes for laser cutting, caving, drilling, welding, soldering, surface treatment, microprocessing, and rapid manufacturing.
About the Author
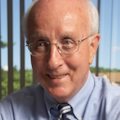
David Belforte
Contributing Editor
David Belforte (1932-2023) was an internationally recognized authority on industrial laser materials processing and had been actively involved in this technology for more than 50 years. His consulting business, Belforte Associates, served clients interested in advanced manufacturing applications. David held degrees in Chemistry and Production Technology from Northeastern University (Boston, MA). As a researcher, he conducted basic studies in material synthesis for high-temperature applications and held increasingly important positions with companies involved with high-technology materials processing. He co-founded a company that introduced several firsts in advanced welding technology and equipment. David's career in lasers started with the commercialization of the first industrial solid-state laser and a compact CO2 laser for sheet-metal cutting. For several years, he led the development of very high power CO2 lasers for welding and surface treating applications. In addition to consulting, David was the Founder and Editor-in-Chief of Industrial Laser Solutions magazine (1986-2022) and contributed to other laser publications, including Laser Focus World. He retired from Laser Focus World in late June 2022.