Additive manufacturing technique builds structural part of spike track shoes
Venetian middle-distance runner Miro Buroni has created and developed spike track shoes with innovative features in terms of production technology and material. For the shoes, dubbed Pleko, Buroni made use of the skills and support of two companies—Diadora (Veneto, Italy) for historical analysis and design, and CRP Technology (Modena, Italy) for the manufacture of the outsole midsole and ribbing using the powder-bed fusion process with Windform SP Carbon fiber-filled composite material.
Starting with a three-dimensional scan of the athlete’s foot, followed by a biomechanical analysis of the act of running and footing through the 3D foot scan, Buroni used selective laser sintering to build the supporting structure of the spike shoe. He selected CRP Technology and its Windform SP composite material, which guarantees excellent resistance even in very thin thicknesses, to create spike shoes that envelop the foot perfectly. This facilitates increased comfort and enhanced performance.CRP Technology manufactured Pleko’s outsole, midsole, ribs, and pins as a single unit. Ribs are originated from under the outsole, in correspondence with the lines of maximum effort during a track race.
“The design and manufacturing technologies, combined with the Windform SP and its mechanical characteristics, made the Pleko track shoes highly innovative, taking the entire, whole project to the highest level of customization and specialization. I am very satisfied with my 3D printed Pleko and Windform SP,” says Buroni.
About the Author
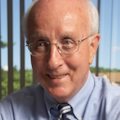
David Belforte
Contributing Editor
David Belforte (1932-2023) was an internationally recognized authority on industrial laser materials processing and had been actively involved in this technology for more than 50 years. His consulting business, Belforte Associates, served clients interested in advanced manufacturing applications. David held degrees in Chemistry and Production Technology from Northeastern University (Boston, MA). As a researcher, he conducted basic studies in material synthesis for high-temperature applications and held increasingly important positions with companies involved with high-technology materials processing. He co-founded a company that introduced several firsts in advanced welding technology and equipment. David's career in lasers started with the commercialization of the first industrial solid-state laser and a compact CO2 laser for sheet-metal cutting. For several years, he led the development of very high power CO2 lasers for welding and surface treating applications. In addition to consulting, David was the Founder and Editor-in-Chief of Industrial Laser Solutions magazine (1986-2022) and contributed to other laser publications, including Laser Focus World. He retired from Laser Focus World in late June 2022.