Manufacturing in India remains a conundrum
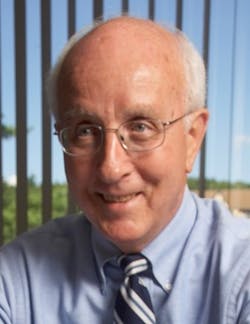
For many years, Industrial Laser Solutions has been fascinated with the manufacturing economy potential of India, mainly for the possibility of this sector as a growth catalyst for industrial laser revenues, as a possible competitor to China (which in Asia and globally, dominates industrial laser sales).
English-speaking India, with a population almost equal to China, seemed to be a leading candidate. So, over the years—starting in 2006—we tapped contacts for their “on-the-scene view of India as a replacement for China.” In 2007 we published, “Unquestionably, India is on a growth trajectory, and the country will emerge as a significant power on the global political and economic stage. China’s world-class infrastructure, with government support smoothing the way for manufacturers, keeps it ahead in global manufacturing. The model for India should focus on competing globally by growing a creative and innovative high-technology manufacturing industry for relatively higher-value products that demand frequent value additions through continued innovation and creativity. This is the area where laser technology can really become acceptable in materials processing applications, which demand in-depth technical knowledge of application engineering.”
We were not prescient, however, as a succession of Industrial Laser Solutions reports remained optimistic, but never delivered expected results. We still believe that India has the potential to be Asia’s dominant market for industrial laser products. And our latest view, as presented by Anant Deshpande, renews our interest (see article).
One of Anant’s projections for laser growth in India is for laser additive manufacturing to be a significant growth opportunity. This leads us to the other feature this month—laser wire directed-energy deposition (DED) has come into contention, based on its higher deposition rate and lower feed stock cost. Stan Ream (EWI) and colleagues show a coaxial laser wire additive manufacturing solution that offers the highest deposition rates of all and discuss the design, performance, and remaining challenges and opportunities for this highly productive technology (see article). Stan points out that coaxial laser wire additive manufacturing has some further developments scheduled, but an eventual deposition rate capability exceeding 100 lb/hr may be sufficient to expedite commercialism of this technology.
About the Author
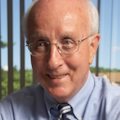
David Belforte
Contributing Editor
David Belforte (1932-2023) was an internationally recognized authority on industrial laser materials processing and had been actively involved in this technology for more than 50 years. His consulting business, Belforte Associates, served clients interested in advanced manufacturing applications. David held degrees in Chemistry and Production Technology from Northeastern University (Boston, MA). As a researcher, he conducted basic studies in material synthesis for high-temperature applications and held increasingly important positions with companies involved with high-technology materials processing. He co-founded a company that introduced several firsts in advanced welding technology and equipment. David's career in lasers started with the commercialization of the first industrial solid-state laser and a compact CO2 laser for sheet-metal cutting. For several years, he led the development of very high power CO2 lasers for welding and surface treating applications. In addition to consulting, David was the Founder and Editor-in-Chief of Industrial Laser Solutions magazine (1986-2022) and contributed to other laser publications, including Laser Focus World. He retired from Laser Focus World in late June 2022.