High-power coaxial wire laser directed-energy deposition: An update
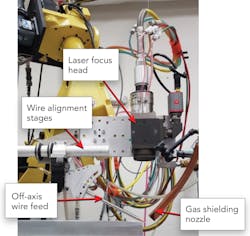
As additive manufacturing technologies have continued to emerge and grow at a remarkable pace, EWI (Columbus, OH) has identified a specific sector that is less well developed and more difficult to address, but nonetheless increasing in interest. Specifically, this area is high deposition-rate metal additive manufacturing that involves the building of much larger structures than are commonly available in today’s metal additive manufacturing world.
EWI’s early experiences with large object builds using laser “blown powder,” electron beam with wire, and gas metal arc welding additive manufacturing techniques had clearly identified multiple challenges and opportunities. So, nearly two years ago EWI committed internal R&D funding to the exploration and development of a high-power, high deposition rate, laser solution for the large object additive manufacturing objective. This report follows an earlier one from a year ago (see http://bit.ly/CoaxialAdditive2020) and adds additional new information, insight, and identification of remaining challenges for this important—and still emerging—additive manufacturing technology.
Background
Additive manufacturing in dozens of forms continues to appeal to designers, manufacturers, and even hobbyists. Materials used among the many additive manufacturing technologies range from polymers, to sand, to metals, and more. Within the metal additive manufacturing group, laser powder-bed fusion (LPBF) has attracted the most attention, and more LPBF systems have been produced than any other metal additive manufacturing type. The attraction and apparent simplicity of its “CAD-to-part” production concept cannot be overstated.
While many important details of LPBF continue to be resolved, its overall stimulus for other additive manufacturing solutions has been considerable. Most significantly, the demand for higher deposition rate metal additive manufacturing has driven increased attention toward directed energy deposition (DED) solutions, using both traditional arc welding, electron beam, and laser techniques for metal fusion. Looking more closely at the laser DED techniques, they can be divided into two categories—specifically laser metal deposition (LMD), also known as “blown powder” DED, and wire-based methods for metal delivery, with the latter being the least developed of all.
Why wire and how to melt it?
Well before there was additive manufacturing, there was metal cladding using arc-based processes for the heating sources. The earliest gas metal arc welding (GMAW) additive manufacturing process patented (U.S. Patent #1,533,300) in 1925 was used to create “various articles of an ornamental and useful nature.” Back then, it was not called “additive manufacturing,” but it certainly fits today’s definition.
Despite such an early start, the GMAW DED process has primarily been used for repair, corrosion protection, and the creation of wear-resistant surfaces. Now, GMAW DED has come back into play in the additive manufacturing world, and laser powder DED is being used to create entire objects. The latter DED solution has even been integrated into machine tools that include milling and turning capabilities to achieve final, precision-machined part dimensions. So, why is wire becoming increasingly interesting for DED additive manufacturing?
First and foremost, all forms of additive manufacturing are becoming more interesting and well accepted, and industries that have previously dismissed additive manufacturing solutions as novelties, unworthy of consideration for their large objects, are taking a much closer look. Aerospace, transportation, metal forming, and Navy applications are among those sectors attracting attention for laser additive manufacturing of larger parts, and the choice between powder vs. wire as the source metal is quite clear, as follows:
- Wire is much more economical per weight than powder
- Wire utilization efficiency is much higher than powder
- Wire DED is far less “messy” than powder deposition
- Wire doesn’t present explosive or respiratory issues
On the other hand, wire has its own deficiencies:
- Wire is more challenging to heat/melt than powder, using a laser as the heating source
- Wire delivery and straightness (or lack thereof) can be problematic
- Wide variations in wire surface emissivity make process development more challenging
Delivery of metal wire to a laser processing zone has been practiced in laser brazing and laser welding for decades, and the wire delivery direction for those applications is almost always aligned with the processing direction. Therefore, most initial laser wire DED developments also used that same alignment of wire feed direction and process travel direction. The off-axis alignment of wire feed direction (see Fig. 1) facilitates laser heating/melting, but it also complicates the additive manufacturing process by requiring articulation of the wire feed mechanism as well as all the associated support cabling and tubing during part building—a significantly challenging task for robotic motion in a large additively manufactured part build.
The alternative, omnidirectional approach for laser wire DED is to feed the wire normal to the work surface, while delivering the laser power onto the wire circumference. This “coaxial” approach has been introduced by numerous laser systems builders, additive manufacturing systems manufacturers, and optics suppliers, including Precitec, Laser Mechanisms, Fraunhofer, Meltio, and others, as well as EWI. (Many examples are easily found with a Google search for “coaxial laser wire DED”.)
Coax wire DED solution
Most of the currently available “coax” wire DED solutions use multiple, individual laser focusing elements to heat and melt the wire and the work surface. Each of typically three beams must be precisely located on the wire outside diameter, and the wire must be straight and unwavering. In the EWI design, the laser beam is delivered in a truly coaxial manner to the wire circumference (see Fig. 2).This laser wire DED concept allows very high-power laser use and has been tested up to EWI’s current laser power capability of 20 kW. The two reflective beam-shaping optics were designed by Dr. Craig Walters and produced by II-VI Incorporated. These optics are water-cooled and far from the work zone, allowing the aero window to protect them without the use of additional cover windows. Optical performance and raw melting capability using this initial design was found to be exceptional:
- Tested to 20 kW
- Power delivery: 94% of fiber power
- Stainless steel wire, 1.6 mm diameter
- Wire feed rates to 855 ipm
- Melting rate performance: 46 lb/hr
- Melting efficiency: 36 mm3/kJ
The metal deposition rate for the 308 stainless steel “wall” build example in Figure 4 is 28 lbs/hr, which is more competitive with typical GMAW additive manufacturing build rates. The laser DED build is exceptionally clean metallographically, and metal fusion to the base metal and between passes is complete.
Conclusions and recommendations
- EWI’s laser wire DED additive manufacturing solution has demonstrated one of the highest build rates in additive manufacturing.
- The optical concepts in this coax design offer a wide range of wire illumination options.
- The eventual deposition rate capability for this laser DED concept may exceed 100 lb/hr.
- Numerical modeling of heating/melting rates and deposition flow dynamics is needed.
- Many other wire materials, wire configurations, laser wavelengths, and laser powers remain to be explored and implemented.
ACKNOWLEDGEMENTS
Thanks and credit go to EWI’s laser coax additive manufacturing development team, including Jacob Hay, Dean Langenkamp, Mark Mohler, Dr. Craig Walters, Stan Ream, and II-VI Incorporated.
About the Author
Stan Ream
Technology Leader, Lasers and Fuel Cells at EWI
Stan Ream is an internationally recognized expert in industrial lasers, process development and analysis, and manufacturing systems design and performance. As laser technology leader at EWI (Columbus, OH), Stan focuses his experience on solutions to the joining challenges facing all EWI industry sectors.
Jacob Hay
Applications Engineer - Laser Processing at EWI
Jacob Hay is Applications Engineer - Laser Processing at EWI (Columbus, OH).
Craig Walters
President, Craig Walters Associates
Craig Walters is President of Craig Walters Associates (Powell, OH).