Will copper welding be the catalyst for laser revenue?
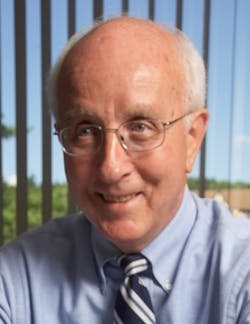
In my laser market review last month, I wrote about the current opportunities for industrial laser material processing (see http://bit.ly/ILS-LaserMarket21). In the forecast for 2021, “Modest growth of nearly 5% is expected to get total industrial laser revenues back near the $5.6 billion pre-COVID-19 levels.” This projection was based on small growth in lasers for welding/brazing revenues to about $719 million or 13% of total laser revenues, not quite up to 2019 pre-COVID-19 shares.
This raises the question of the possibility of a ‘killer app’ such as battery welding for e-mobility, boosting laser welding to closer to 20% of total laser revenues—a position never before attained.
I sounded this out on the Industrial Laser Solutions Editorial Advisory Board and received the following comments:
- Readers of this month’s features on welding copper for electric vehicle (EV) batteries can make their own call
- It certainly has caught more attention than any other new laser welding thing
- The rate of emergence of e-mobility laser applications certainly outpaces the speed of sheet metal cutting
- The EV industry will definitely put laser welding firmly on the revenue map, (finally) moving it out of the shadow of laser cutting, and may provide the springboard for the laser welding revolution
- Batteries won’t be so singular on their preferred laser type, like fiber lasers used in cutting
- Welding of copper is one of the fastest growing laser welding applications areas because of the tons being used in e-mobility
- Very good beam quality, high-power blue lasers at 2 kW are good for remote welding battery packs
- With the China EV market back on track, and OEMs such as VW seemingly betting the farm on EVs, long-term growth is promising
- Batteries won’t be so singular on their preferred laser type like it is in cutting
- Trumpf made a bet on battery welding some years ago already—I guess they are sure to win
Meanwhile, our contributors this month say:
- Advances in weld speed and quality enable new efficiencies in battery fabrication, and e-mobility applications
- Copper welding with a new type of adjustable-ring-mode (ARM) fiber laser demonstrates this increased weld speed while retaining the inherently advantageous characteristics of fiber lasers.
In this issue, Jean-Michel Pelaprat and colleagues at Nuburu speculate on how low-operating-cost Nd:YAG lasers replaced CO2 in certain applications. Then, fiber lasers displaced CO2 marking/cutting. Now, the blue laser is reproducing that pattern in copper processing (see article).
Then, Klaus Kleine and Falk Nagel at Coherent suggest that new high-brightness ARM fiber lasers avoid surface quality sensitivity and process instability that have limited the use of fiber lasers for copper in the past, and can be an effective solution for demanding copper welding applications in e-mobility (see article).
About the Author
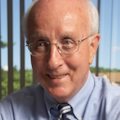
David Belforte
Contributing Editor
David Belforte (1932-2023) was an internationally recognized authority on industrial laser materials processing and had been actively involved in this technology for more than 50 years. His consulting business, Belforte Associates, served clients interested in advanced manufacturing applications. David held degrees in Chemistry and Production Technology from Northeastern University (Boston, MA). As a researcher, he conducted basic studies in material synthesis for high-temperature applications and held increasingly important positions with companies involved with high-technology materials processing. He co-founded a company that introduced several firsts in advanced welding technology and equipment. David's career in lasers started with the commercialization of the first industrial solid-state laser and a compact CO2 laser for sheet-metal cutting. For several years, he led the development of very high power CO2 lasers for welding and surface treating applications. In addition to consulting, David was the Founder and Editor-in-Chief of Industrial Laser Solutions magazine (1986-2022) and contributed to other laser publications, including Laser Focus World. He retired from Laser Focus World in late June 2022.