Cutting applications for carbon dioxide lasers with acousto-optic modulators
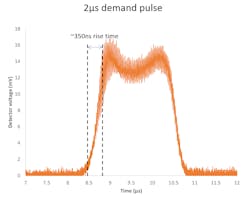
In recent years, South Korean companies have been dominant in the display industry, particularly in the organic light-emitting diode (OLED) market. Additional investments have also recently started with Chinese companies, and this trend is expected to continue for three to four years. With the expansion of the display industry, ultrashort-pulse (USP) laser markets have grown as a result of applications such as OLEDs, which require higher laser power and more-precise processing quality. This industry is prepared to pay for better laser-based solutions, which has fueled the demand for shorter-pulsed carbon dioxide (CO2) lasers for film cutting applications. One of the key features required in the market is to minimize the heat effect on the material during the cutting process.
In order to address this demand, Luxinar (Kingston upon Hull, England) has launched the SR AOM CO2 laser range, which integrates an acousto-optic modulator (AOM) and has a rise/fall time of <1 μs. The SR AOM lasers minimize unnecessary heat energy while processing when compared with traditional CO2 laser sources, which typically produce longer pulse rise/fall times of approximately 60 μs.
In addition to the display industry, the electronic manufacturing services (EMS), automotive, and flexible packaging industries demand a reduced heat-affected zone (HAZ) for laser processing, with microcontrolled processes becoming more common. The above lasers could be a possible solution for many of these applications.
The most important feature of the SR AOM series is its exceptionally fast optical rise/fall time capability of <1 μs. Without the AOM function, a typical optical rise and fall time of a CO2 laser is approximately 60 μs. While this is acceptable for many laser processing applications, it can lead to the creation of HAZ on thin polymer-based materials. This is unacceptable for many of the materials used in the electronics industry.
Figure 1 shows the typical 2 μs demand pulse shape that has approximately 350 ns pulse rising time. This short rise/fall time would help to minimize HAZ.
The clear benefit of the short rise/fall time is in cutting thin film. A wide range of thin films are used in many different industries, including display, automotive, EMS, lighting, and flexible packaging. An AOM-integrated CO2 laser can bring a higher-quality cutting edge with less HAZ compared to a standard pulsed CO2 laser.
Figure 2 shows the results of cutting polarization film (3-layer, 0.23 mm thick) using a standard CO2 laser and a CO2 laser with AOM. The AOM-integrated CO2 laser creates approximately 30% less HAZ and a significantly better edge quality.The picture on the right in Figure 3 shows the result achieved using the SR 25 AOM operating at 9 μm and clearly demonstrates the improvement possible when compared with the results using a Luxinar SCX 35 operating at 9 μm (left). The upper and lower protection film layers are dramatically improved with a significantly less melted area. A more important benefit relates to the adhesive silicone layer as it no longer sticks to the neighboring layers, creating an easy-to-peel protection film layer. In many cases, heat-sensitive film applications such as projected capacitive film can be cut using picosecond UV laser solutions—however, a CO2 laser with integrated AOM can achieve similar results with significantly lower investment and maintenance costs.
Figure 4 shows an application where thin film technology is utilized. Applications include touchscreens, optical clear adhesive (OCA) films, LCD/OLED tablet-related films, vehicle dashboard instrumentation, and foldable displays.Another interesting application is polymer-dispersed liquid crystal display (PDLCD) film cutting. PDLCD has a structure where polymers and liquid crystals are mixed at a certain ratio between polyethylene terephthalate (PET) and indium tin oxide (ITO). When inactive, the liquid crystal droplets scatter and as they permeate the screen, this results in a turbid (opaque) state. When a voltage is applied, the liquid crystal droplets align, allowing light to pass through. This essentially turns the screen from a transparent to a non-transparent state, and is frequently used for office meeting room windows to provide privacy.
PDLCD is also becoming more common in other sectors. Beyond its typical use in the construction industry (for window coatings), it can be employed in a large range of other applications such as transportation, advertising screens, art, culture, and in other products and industries that use display technology. PDLCD is commonly used in the automotive industry for car sunroofs and in the electronics sector, where display technology is often combined with microprocessor-based devices.
Due to the heat-sensitive ITO layers in PDLCD film, discoloration is an issue when cutting with traditional CO2 laser technology. The cutting process with SR-based AOM 9 μm systems can, however, minimize this discoloration as well as produce an extremely clean cut-edge quality. The fast rise/fall time created by the unit of <1 μs results in minimal heat energy transfer into the material.Other potential markets
The AOM-based laser may bring benefits to the flexible packaging industry due to its short pulse rise/fall time capabilities and its superior pulse-to-pulse control feature, which can help to process materials more precisely with less HAZ. Modified atmosphere packaging (MAP), where plastic film is laser-perforated to keep food fresh, could also be a well-matched application for this system.
Applications such as label cutting and selective cutting are potential markets for the SR AOM range, too. Due to its power stability and very short rise/fall time, its precision process control can greatly improve the consistency of the scribing process.
Summary
As part of the well-established SR series from Luxinar, the SR 25 AOM 9 μm CO2 laser provides superior pulse-to-pulse control and output power stability, and has a fully integrated RF PSU, control driver, optical optimization, and AOM. The laser series is ready for mass production together with easy integration to enable clean and high-quality laser processing, low running costs, and maintenance-free operation.
About the Author
Patrick Kim
Regional General Manager (Korea), Luxinar
Patrick Kim is Regional General Manager (Korea) for Luxinar (Suji-gu, South Korea).