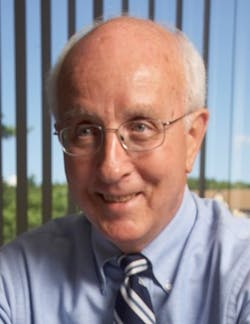
Who would have thought my 50th year in industrial laser material processing would get topped by bigger news, especially a bug from Wuhan! Well, it took a pandemic, stock market crash, canceled sports events, and country lockdowns to do it.
I’m sort of inured to this, as I’ve been through three others: the Hong Kong Flu Pandemic (1968); the Asian Flu (1956-1958), which knocked me out for 4 weeks; and the Swine or Bird Flu of 2009, which followed me all over China one year. But this is the first time I’ve been isolated, with routine travel, shopping, entertainment, and dining out eliminated.
The governor of my state, Massachusetts, took matters into his own hands while the federal government postured, pondered, and procrastinated in the face of a proven disaster. We are essentially locked down except for very limited public appearances for food and medications. Our local hospital has advised us we are persona non grata, a burden on an overworked and courageous staff. And the joys of life like attending the theatre or visiting an art museum are verboten.
I’m unconcerned about being housebound since I’ve worked from home for the past three decades and I’m no stranger to solitude when working in my home office. This is a time of some relief, as I don’t have to worry about interacting with COVID-19 carriers. The governor frowns on gatherings of 10 or more, so there goes our annual St. Patrick's Day dinner.
My peers at the New Hampshire office of Endeavor Business Media, the publisher of Industrial Laser Solutions, are working remotely as well—and because we are a digital publication, they are, for the most part, equipped to work from home.
So, do not be concerned—the May/June 2020 issue of Industrial Laser Solutions should reach you on schedule, thanks to our online deployment process. If you are housebound, you’ll enjoy this issue, which has laser welding as its theme.
I actually started in laser processing after my company, which manufactured a variety of welding equipment, under my urging commenced a search for the next automated fusion welding process. We, the company that in 1886 (way before my time) invented and commercialized resistance spot welding, had a reputation for welding innovations (butt welding, projection welding, seam welding, welding copper to aluminum, flash butt welding, wire fabric welding, three-phase welding aluminum, low-voltage, movable gun electron bean welding, and programmed inert gas multi-electrode welding) and was looking for the next technology breakthrough.
I came across a company that had a technology solution looking for a problem—a solid-state laser. I had a problem looking for a solution, which was how to use a beam of energy to fusion weld metals. I already tried a beam of electrons, which worked in a vacuum environment for high-energy welding. I wanted high-energy density in air and photons from a laser seemed a match. I found the laser beam process had been proven by others—all that was lacking was a commercial product that could be accepted for serial manufacturing.
I joined this company, which happened to have a problem spot welding precious metal eyeglass frames, and after internal development of a laser that could function and produce output energy repeatedly and reliably in a workplace environment, we were on our way with a production laser welder. The frame welding operation was not cost-effective, as were a long list of other industrial applications. Laser welding was great technically but hard to justify, mostly due to the high cost of generating photons with sufficient energy to join metals. Over time, technology changes narrowed the cost/function gap and laser welding became a cost-effective welding process, representing about 15% of annual laser revenues.
Much work has gone into increasing lasers’ share of total sales revenues, but this welding process is still very part specific and successfully proving it in a timely (low cost) manner is now the goal of many companies. In the upcoming May/June issue, Industrial Laser Solutions is doing its part with five state-of-the-art articles on laser welding for e-mobility (batteries), composite materials, stainless steel, copper-brass-gold, and dissimilar metals.
You won’t want to miss this welding theme issue, so ensure that you receive it first by subscribing today (it’s free; industrial-lasers.com/subscribe).
About the Author
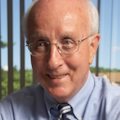
David Belforte
Contributing Editor
David Belforte (1932-2023) was an internationally recognized authority on industrial laser materials processing and had been actively involved in this technology for more than 50 years. His consulting business, Belforte Associates, served clients interested in advanced manufacturing applications. David held degrees in Chemistry and Production Technology from Northeastern University (Boston, MA). As a researcher, he conducted basic studies in material synthesis for high-temperature applications and held increasingly important positions with companies involved with high-technology materials processing. He co-founded a company that introduced several firsts in advanced welding technology and equipment. David's career in lasers started with the commercialization of the first industrial solid-state laser and a compact CO2 laser for sheet-metal cutting. For several years, he led the development of very high power CO2 lasers for welding and surface treating applications. In addition to consulting, David was the Founder and Editor-in-Chief of Industrial Laser Solutions magazine (1986-2022) and contributed to other laser publications, including Laser Focus World. He retired from Laser Focus World in late June 2022.