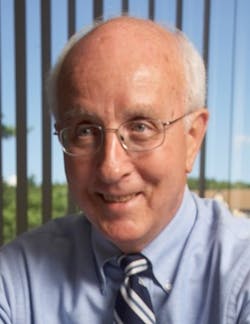
As this is being written, the United States is proposing potential tariff increases, directed mainly at China and with one a penalty on Mexico for control of border infractions, that have roiled international stock markets. The situation and its effects on global manufacturing are very fluid, not to mention the impact on the wallets of U.S. consumers, because tariff increases are usually passed on in the selling prices of imported goods—foods, appliances, auto parts, and even the vehicles themselves.
In addition, the U.S. Executive Branch is rattling swords in the mid-East with a show of strength, warship movement in the Persian Gulf is underway against Iran, and there is also talk of an on-the-ground response.
All of the above are predicted to change the global economic picture, and fallout could be a sharp decrease in 2019 gross national product (GNP). The situation is very unpredictable and, as we are entering the second half of a so/so first half, gloomy predictions are common. One can speculate that more thoughtful actions will emanate from Washington, but the political scene surrounding an embattled leadership is complicating moderate policies. Since this publication is focused on the world of manufacturing, I call your attention to the title on the front cover—we are concerned that a bright future for industrial laser material processing might be tarnished by negative changes.
And this would be too bad, as this issue of Industrial Laser Solutions, with a continuing theme on e-mobility welding, presents significant contributions that can have lasting effects on future manufacturing. Frank Gäbler and Matthew Philpott (Coherent) report on a new welding technology that improves bonding applications encountered in e-mobility manufacturing, delivering welds showing reduced spatter and improved metallurgical characteristics with highly reliable bonds in battery and motor production (see article).
Fiber lasers are the tool of choice for the fast-growing market in e-mobility. Chris Galbraith (IPG Photonics Canada) says recent developments in laser weld measurement technology provide the “eyes and ears” needed to increase yields, reduce dependence on costly downtime, and boost confidence in welding results from process development through to production (see article).
In Industry 4.0, lasers play a dominant role, as it is possible to produce a part directly from a digital model by contactless processing. Markus Kogel-Hollacher (Precitec) says this allows monitoring processes with smart optical coherence tomography (OCT) devices—a key issue in Industry 4.0 (see article).
Staying in the auto industry, Kohei Yanaka describes laser-clad valve seat technology developed by Toyota, in which wear-resistant alloy directly deposited onto cylinder head valve seats enhances knocking resistance and improves combustion efficiency by increasing design flexibility around the ports (see article).
The mobile device display industry increasingly utilizes thinner glass, strengthened glass, curved corners, contoured shapes, and cutouts. George Oulundsen and colleagues (Coherent) demonstrate a new filamentation and CO laser separation process that is an important tool in meeting production requirements (see article).
And our man in India, Anant Deshpande, encouraged by the reelection of a progressive government, expects the economy to grow at 19% CAGR by 2020. Industrial laser applications, especially in micromachining and additive manufacturing, have opened new market segments, suggesting that India could become one of the world’s largest markets for lasers (see article).
Let’s be optimistic and anticipate that the successes of the above will end in a positive review of a more-stable 2019 economy.
About the Author
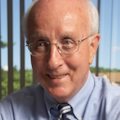
David Belforte
Contributing Editor
David Belforte (1932-2023) was an internationally recognized authority on industrial laser materials processing and had been actively involved in this technology for more than 50 years. His consulting business, Belforte Associates, served clients interested in advanced manufacturing applications. David held degrees in Chemistry and Production Technology from Northeastern University (Boston, MA). As a researcher, he conducted basic studies in material synthesis for high-temperature applications and held increasingly important positions with companies involved with high-technology materials processing. He co-founded a company that introduced several firsts in advanced welding technology and equipment. David's career in lasers started with the commercialization of the first industrial solid-state laser and a compact CO2 laser for sheet-metal cutting. For several years, he led the development of very high power CO2 lasers for welding and surface treating applications. In addition to consulting, David was the Founder and Editor-in-Chief of Industrial Laser Solutions magazine (1986-2022) and contributed to other laser publications, including Laser Focus World. He retired from Laser Focus World in late June 2022.