Fraunhofer ILT showing laser-treated steel for automotive apps
Aachen, Germany - At EuroBlech later this month (Oct. 23-27, Hannover, Germany), a new technique will be demonstrated for local heat treatment of high-strength steels to soften the material so that it can be better formed into components.
Automakers continuously seek ways to reduce weight in vehicles, mainly to meet more rigid fuel-efficiency mandates. Much development work has gone into new materials and processing techniques to reduce costs and materials usage in areas such as the body-in-white (i.e. the vehicle's welded-together skeletal structure, before adding the engine and moving parts and subassemblies and trim). Tailored blanks have advanced these efforts by paving the way for sheet metal with locally tailored properties.
Another way to is using stronger steels with lower metal thicknesses that don't impair function of the parts. Toward this end, a new approach has been developed by a consortium of automakers, steel producers, a tool and laser suppliers, and research institutes -- including Fraunhofer Institute for Laser Technology (ILT), which will be showing the work at EuroBlech -- working under the "LOKWAB" project funded by the German Federal Ministry of Education and Research (BMBF). (The process apparently was presented earlier this year at the SPIE High-power Laser Materials Processing conference.)
A fiber-coupled 10 kW high-power diode laser projects a rectangular beam (90 mm width) onto the workpiece using a special optic. Large areas can be softened in a single pass, with the beam profile adjustable thanks to a zoom optic. Temperature monitoring in coaxial alignment with the laser beam enables control of the heat treatment.
Their technique involves locally softening sheet metal using heat input, allowing the material to be treated using the laser so it can be deep-drawn much further at the modified points without generating cracks. The heat-treating method also works on galvanized sheet metal without impairing corrosion protection, and on press-hardened components to improve joinability via spot welding.
As an application demonstration, the group applied the heat-treatment process to ultrahard-steel (MS-W1200) to form into B-pillars. In a crash test the B-pillar "proved clearly superior" to one made from high-strength steel with identical thickness (CP-W800).
The new technique also paves the way for material and component-tailored solutions using local laser heat treatment of sheet metals above and beyond softening: e.g., tempering, recrystallization, and hardening. Graduated properties can be produced across the sheet metal thickness. Fraunhofer ILT and partners determined that the laser technique proves superior to conventional technique in areas across the entire manufacturing process chain, particularly where flexibility is required.
About the Author
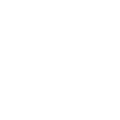
James Montgomery
Associate Editor
James manages editorial production for news (online and print) and newsletters, as well as the magazines' new product sections. Jim has 13 years’ experience in producing Web sites and e-mail newsletters in various technology markets for CNet, ZDNet, Digital City Boston/AOL, and KM World.