Laser welding improved with vision sensors
Schramberg, Germany -- Leading laser system manufacturer Trumpf is integrating vision technology into some of its laser welding machines to improve flexibility and accuracy and speed up the system output.
Laser welding is employed for precise joining of components, often of different materials, in a number of industries: automotive infrastructure and components, medicaldevices, shipbuilding, aircraft, and engine turbines.
Trumpf chose to integrate vision sensor technology from Cognex Corp. into the programmable focus optic (PFO) in some of its laser welding machines, to enable automatic positioning to match workpiece position and size and determine coordinate transformation data. Instead of using grey-shade correlation, software images the geometric structures of objects (edges, dimensions, shapes, angles, curves, shading) and compares them to the real-time image to locate the object. In standard applications, complete image evaluation takes ~180 msec. Images and coordinate data are transferred via Ethernet to the laser's FDP server. The vision system integrates with the laser server's fault diagnosis using WinLas software.
The vision system eliminates the need for clamping and positioning devices, as well as an image processing PC. The system can be mounted straight onto the PFO to save space. Waste and production costs are also reduced, according to the companies. They vision-enables systems are also user-friendly for operators without prior vision experience.
Trumpf has more than ten systems in the field with the new vision system, all of which are retrofits or beta systems. In addition, potential new customers can send sample parts to Trumpf and integration partner Rohwedder AG Vision, to determine viability of the project (system reliability, aiming accuracy and μm tolerance, etc.) and test under production conditions.
About the Author
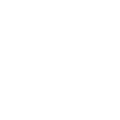
James Montgomery
Associate Editor
James manages editorial production for news (online and print) and newsletters, as well as the magazines' new product sections. Jim has 13 years’ experience in producing Web sites and e-mail newsletters in various technology markets for CNet, ZDNet, Digital City Boston/AOL, and KM World.