Rolls-Royce granted patent for laser-brazing BLISKs
Dahlewitz, Germany -- Rolls-Royce Deutschland Ltd & Co KG has been granted a US patent (#8,242,406) for a method of manufacturing BLISK turbine engine components by laser brazing or joining.
BLISKs are rotor disks with integrated compressor blades, typically produced with conventional manufacturing processes such as five-axis milling of solid material. (Earlier this year Germany's Fraunhofer Institute for Laser Technology [ILT] was recognized for its alternative BLISK-making method to using laser additive manufacturing, which it says significantly cuts down on materials usage and production time.)
In its patent description, the company explains the drawbacks of conventional methods to make BLISKs. Integrating the bladed rotors using linear friction welding is restricted by component design, large-sized blades, and a complex fixture. Conventional fusion welding, meanwhile, doesn't meet required strength properties to avoid weld-area cracking. Moreover, these joining processes require the rotor disk and blade be made of the same (or similar) materials -- even though the blade and disk properties may differ in how they have to deal with factors such as fatigue, erosion, and thermal loading.
Rolls-Royce's proposed new method uses laser brazing to make BLISKS. Brazing powder is jetted into the laser beam and shields the blade, so that only the brazing metal is heated and melted. The disk material is molten in the joining area and alloys with the similar brazing metal; the blade material is not melted, and connects to the solidifying, dissimilar brazing metal by adhesion.
About the Author
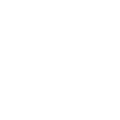
James Montgomery
Associate Editor
James manages editorial production for news (online and print) and newsletters, as well as the magazines' new product sections. Jim has 13 years’ experience in producing Web sites and e-mail newsletters in various technology markets for CNet, ZDNet, Digital City Boston/AOL, and KM World.