Laser welding plastic was highlight of MDM East
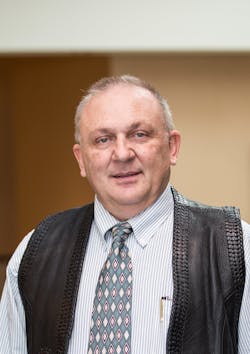
I was asked to write a BLOG for Industrial Laser Solutions and charged headlong into it a couple of months ago without even knowing what a BLOG was or is. So, if we turn to the web, we find the definition: “What's a blog? A blog is a personal diary. A daily pulpit. A collaborative space. A political soapbox. A breaking-news outlet. A collection of links. Your own private thoughts. Memos to the world. Your blog is whatever you want it to be. There are millions of them, in all shapes and sizes, and there are no real rules.” Ok, I can dig those conditions, especially the 'no real rules' part, although my editors might not agree! Anyway, on to the topic of this blog: the Medical Device Manufacturing show …
This is the second (and last!) year that this conference was held in Philadephia. It was moved from NYC during construction on the Jacob Javitz Center, and it will return again next year to the city where it had been located for many years. Based on the feedback from vendors and personal observations on the show floor, it seems a good move. The show was comparatively slow both last year and this year, closing at 4 pm presumably because traffic in and around the city is so horrible. I grew up in PA just north of Philly, and we always heard as kids that the roads in PA are the worst in the nation; it seems like some things never change. One thing positive is the location of the convention center directly across the street from the Reading Terminal Market – a place where you can get anything and everything to eat and is the home of the famous Philly Cheese Steak. Last year, I met more customers at the market than on the show floor!
Besides the usual micromachining and marking applications, the thing that really caught my interest was the plastic welding. IPG Photonics has been promoting a 2 micron (1940 nm to be exact) wavelength laser recently. According to Dr. Tony Hoult of IPG, this laser is of interest because of its higher absorption than at 1 micron wavelength of many materials, such as water and most if not all hydrocarbons. Alternatively, most semiconductors absorb less. [Note that Dr. Hoult, a member of the ILS Editorial Board, will be writing an upcoming feature in Industrial Laser Solutions on 2 micron fiber applications.]
Most plastic welding applications require a transparent top layer and an absorbing bottom layer in order to make the weld. If both layers are equally transparent, then sometimes an absorbing adulterant is placed in between to initiate laser welding. With the 2 micron laser, it has been shown that even two otherwise ‘transparent’ materials can be welded cleanly, quickly and efficiently – the so called Clear-Clear weld. As in all welding applications, the best joints are made when the materials are in intimate contact with each other, so fixturing, jigging, and tooling are very important to the success.
A well known player, LPKF from Germany, unveiled its new PrecisionWeld product line at the show. It is specifically designed for fine microfluidic weld seams with typical weld widths of 100 microns and repeatability of 10 microns. The tool uses an IPG Thulium fiber laser and has options for part handling and in line inspection of the weld. Using differential pressure clamping, parts can be held in an air-tight grip, assuring 100% contact between the upper and lower plates. By also holding the focus very close to the weld plane, a perfect weld can be made. This technology is extremely useful in manufacturing microfluidic devices, lab-on-a-chip devices, and atomizers. The photo above, courtesy of LPKF, shows an atomizer that dispenses precise amounts of active ingredients.
I am always interested in hearing your thoughts concerning laser micromachining, the laser industry, comments on entrepreneurial endeavors, etc. AND … we are always looking for fresh, publishable material. Please feel free to contact me at [email protected].
About the Author
Ron Schaeffer
Ron Schaeffer, Ph.D., is a blogger and contributing editor, and a member of the Laser Focus World Editorial Advisory Board. He is an industry expert in the field of laser micromachining and was formerly Chief Executive Officer of PhotoMachining, Inc. He has been involved in laser manufacturing and materials processing for over 25 years, working in and starting small companies. He is an advisor and past member of the Board of Directors of the Laser Institute of America. He has a Ph.D. in Physical Chemistry from Lehigh University and did graduate work at the University of Paris. His book, Fundamentals of Laser Micromachining, is available from CRC Press.