CLEO 2013: Interesting new laser found
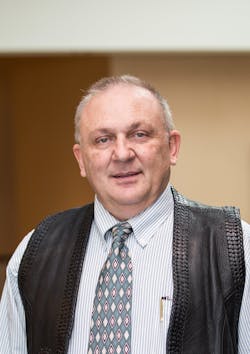
CLEO, the Conference on Lasers and ElectroOptics, is probably the longest-running major laser show. I remember going there as my first trade show almost 30 years ago. This was THE show, the place where all new products got introduced. Historically, it has been held in alternating years on the West and East Coasts, but word has it that it will stay in San Jose for the foreseeable future and will not be going back to Baltimore, where it has been every other year for a long time. This is obviously due to shrinking attendance and more importantly vendor participation. An interesting tidbit is that the SPIE Defense show (the subject of a previous Blog) moved from Florida to Baltimore a few years ago in order to increase attendance, while CLEO may move away from Baltimore.
The conference is not the place for applied laser work — that is handled at conferences like ICALEO and Photonics West in the US. However, it is still a place to talk about lasers and laser technology. Also, at least this year, it is kind of hard to reveal new lasers when both Photonics West and the Munich laser show preceded this event. There is only so much new that can be brought out within a couple of months.
Nevertheless, sometimes one can find interesting things while attending CLEO and other trade events. For instance, I was approached to take a look at an interesting new laser and some preliminary results. The photo shows a laser hole drilled in 3/16-in. (4.76 mm) stainless steel. The scale (500 micron) is included in the picture to calculate the aspect ratio. My new colleague was particularly interested in my thoughts on the lack of a heat affected zone, but I was much more interested in the extremely high aspect ratio! There does not appear to be any heat affected zone in the bottom 90% of the depth of the hole. It took about 15 sec to drill this hole in 3/16-in. stainless steel by operating the laser at 50% of the maximum power. The exit hole diameter is about 40 microns, the taper about 1.2 degrees, and the resulting aspect ratio is about 115:1! A thicker sample was also drilled (0.25-in. or 6.35 mm) in stainless steel, which took about 32 sec. Check out the You Tube video from Sparkle Optics that shows the drilling: https://www.youtube.com/watch?v=Q2AyeYpAv5k.
This video was made for drilling a 0.25-in. stainless steel sample with a very crude and simple laser machining set-up. The company expects to do remarkable things with proper laser machining set-up and software. There are many applications for this type of high-aspect-ratio drilling, particularly for fuel injectors, spinnerets and aircraft engine components. More information can be found at www.sparkleoptics.com. So, keep attending the shows and conferences and keep your eyes open as you never know what will pop up unexpectedly!
I am always interested in hearing your thoughts concerning laser micromachining, the laser industry, comments on entrepreneurial endeavors, etc. AND … we are always looking for fresh, publishable material. Please feel free to contact me at [email protected].
About the Author
Ron Schaeffer
Ron Schaeffer, Ph.D., is a blogger and contributing editor, and a member of the Laser Focus World Editorial Advisory Board. He is an industry expert in the field of laser micromachining and was formerly Chief Executive Officer of PhotoMachining, Inc. He has been involved in laser manufacturing and materials processing for over 25 years, working in and starting small companies. He is an advisor and past member of the Board of Directors of the Laser Institute of America. He has a Ph.D. in Physical Chemistry from Lehigh University and did graduate work at the University of Paris. His book, Fundamentals of Laser Micromachining, is available from CRC Press.