Using short-pulse lasers for micromachining
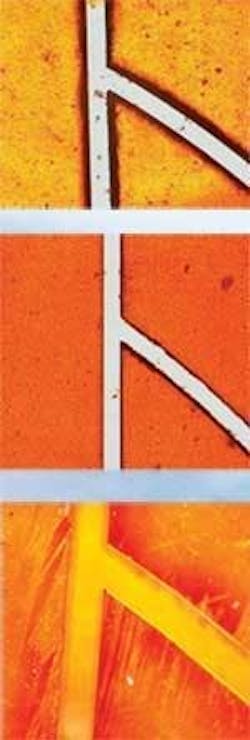
We have previously reported on processing a variety of materials using different lasers (see ILS Dec. 2004, Dec. 2006, Feb. 2007, and Feb. and May 2008). Generally, the shorter the wavelength and the higher the peak power intensity on target, the better the results will be. In fact, wavelength dependence is more important at long pulse lengths in the tens of nanoseconds range. As the pulse length gets shorter, the wavelength dependence is minimized. This article explores some interesting observations related to using shorter-pulse lasers for materials processing and micromachining applications.
As a first requirement, successful micromachining of a material requires that the material efficiently absorbs light at the laser output wavelength. As a rule of thumb in the ultraviolet (UV), successful micromachining requires 50 percent of the laser pulse be absorbed within 0.1 micron depth.
The first lasers reviewed are diode-pumped solid-state lasers. Current applications involve plastic, metal, ceramic, and glass substrates. Until recently, the majority of these applications have been well-served by available lasers with an output wavelength of 355nm and typical pulse duration of 40–60ns or more. But the need for increased miniaturization and the concomitant requirement for better edge quality are pushing the limits for these lasers. Superior resolution and edge quality can be achieved by using shorter (266nm) wavelengths, but this can increase processing costs. In many materials, similar results can be obtained simply by using a 355nm laser with shorter (˜20ns) output pulses.
In this article, we show why this is possible and examine several examples. There may also be an additional cost advantage to using the shorter pulse lasers. Cleaner edges with minimized debris can provide the benefit of not requiring post-processing cleaning.
Both lasers (Coherent Avia and Matrix) are set up optically in a similar fashion—expanding the beam into Scanlab HurryScan 10 or 14 galvos to achieve the smallest spot for about a 4–8in. field. This results in about a 20-micron spot on target. In extensive studies we have shown that, in many materials, comparable results to 266nm processing can be obtained simply by using a 355nm laser designed to produce shorter pulse widths with high beam quality. Specifically, we have found that at around 20ns pulse width or lower, and an M2 lower than 1.3, peripheral thermal effects in these materials drop off significantly. The key is to have a reliable laser with such a short pulse width and high beam quality.
One way to get shorter pulse widths is to lower the pulse repetition rate, but this would slow the throughput for many machining processes. Alternatively, shorter pulse widths can be reached by building a physically shorter laser cavity and also by pumping more energy into the laser crystal. The Matrix family of 355nm lasers deliver 10–20ns pulse widths, high pulse energy stability (noise typically 1–2 percent RMS), and high beam quality (M2~1.2) at pulse repetition rates as high as 80kHz.
Plastics processing
Several polymer materials commonly used in medical devices absorb strongly at 355nm. A standout example is kapton, an excellent candidate that can benefit from a short 355nm pulse. Figure 1 shows typical results on identical samples that have been micromachined with a short-pulse 355nm laser, a longer-pulse 355nm laser, and a 266nm laser. As can be seen, the economic 355nm approach will deliver indistinguishable results and would therefore be the best choice. Mylar absorbs less strongly, but the short-pulse 355nm laser can still deliver almost the same results as a 266nm laser (see Figure 2). So again, the lower cost and higher throughput benefits of the short-pulse 355nm laser would make it the first choice.
With these organic polymers, the UV absorption depends on the bond structure. Materials with double bonds absorb at longer wavelengths including 355nm. But the absorption of highly saturated polymers is limited to shorter wavelengths, so these would require a 266nm laser. The perfect example is Teflon, where the pure material is difficult to machine even at 266nm. Fortunately, most medical device applications use Teflon with colored additives that absorb even in the visible. So here the short-pulse 355nm laser can deliver great results. For Teflon the optimum laser choice strongly depends on what additives are present.
Metals
For most metals, results with the short-pulse 355nm laser are almost as good as with a 266nm laser (see Figure 3.) The fact that the 266nm results are slightly better may be due to the high thermal conductivity of metal negating some of the heat reduction benefits of a short-pulse approach. In most cases this marginal difference will not be critical, and therefore most metal foil applications can be well-served with a short-pulse 355nm laser.
The very short pulse length laser (from Raydiance) has a pulse length of about 500fs, orders of magnitude shorter than the lasers discussed above. The fundamental output is at about 1-micron wavelength. Unfortunately, the energy per pulse is very small (<10µJ/pulse), so galvanometers cannot really be used effectively as it requires a spot size on target of less than 5 microns in order to get sufficient energy density to affect clean material removal. Therefore, this laser beam was delivered through a microscope objective and table motion was used rather than moving the beam—meaning the processing times were long; however, the quality of the processing is exceptional.
Because of their high cost these laser types are normally used in applications where processing quality and enabling new processes are more important than cost or speed requirements. An example is the cutting of detonators for shaped charges (see Figure 4). We have been working with a highly proprietary material that is very explosive upon impact—meaning either a physical impact (hit it with a hammer) or even the impact of a single laser pulse. We are not able to use any of our available lasers except the Raydiance laser, which cuts the material beautifully. This is important as there needs to be a manufacturing method for forming these shaped charges, but then an easy method (hitting with a laser pulse) of igniting them.
In conclusion, shorter pulses produce cleaner results, and wavelength dependence is minimized by going to shorter pulses. We believe that (assuming strong absorption and small spot sizes, i.e. high energy density on target) pulse lengths greater than 20ns will almost always show heat affects, pulse lengths 1ns to 20ns may or may not show heat affects, and pulse lengths less than 1ns in many applications show little or no heat affects.
We can make extremely good quality cuts using femtosecond lasers, but the cost and speed are both issues for high-volume manufacturing. As a reasonable compromise, the available picosecond lasers on the market (as an example, products from Lumera) show both great processing quality (see Figure 5) and reasonably cost-effective processing speeds, although not near as economical as using the commercially available, short-pulse 355nm lasers.
Authors' note:
The above paper mentions companies and products used in our investigations as examples only. This should not be taken to mean that other products with similar specifications will not perform equally as well—or perhaps better.
About the Author
Ron Schaeffer
Ron Schaeffer, Ph.D., is a blogger and contributing editor, and a member of the Laser Focus World Editorial Advisory Board. He is an industry expert in the field of laser micromachining and was formerly Chief Executive Officer of PhotoMachining, Inc. He has been involved in laser manufacturing and materials processing for over 25 years, working in and starting small companies. He is an advisor and past member of the Board of Directors of the Laser Institute of America. He has a Ph.D. in Physical Chemistry from Lehigh University and did graduate work at the University of Paris. His book, Fundamentals of Laser Micromachining, is available from CRC Press.
Gabor Kardos
Gabor Kardos is contract manufacturing manager at PhotoMachining (Pelham, NH).
Scott Murphy
Scott Murphy is an application engineer at PhotoMachining (Pelham, NH).
David Grossman
David Grossman is an application engineer at PhotoMachining (Pelham, NH).