The globalization of industrial laser processes
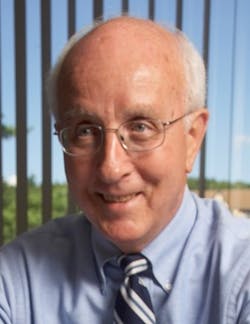
My attention was attracted by the sponsor credit on a favorite public television program promotion by Fisher & Paykel, a manufacturer of major home appliances. Normally, my brain is wired to block these commercials, but this one connected—mainly because my wife and I had visited the New Zealand home plant of this company during a South Pacific lecture tour several years ago.
Our host, the general manager, generously guided us around the plant, pausing to show us a clothes washing machine with a stainless steel drum. My wife admired the drum and complimented the company on its response to many women's complaints about chipped coated-steel washer drums, wishing the company distributed this washer in the US, where she was sure it would be a hit.
As I recall, I asked how the washer drum was fabricated and was walked to the area where hand-built prototypes were being assembled. A lengthy discussion with several engineers revolved around laser welding the seam on the rolled-up stainless steel drum and laser cutting the holes instead of punching.
I've always had a "warm place" for the company, for the way they enthusiastically welcomed two jet-lagged visitors from halfway around the world who unexpectedly dropped in on an otherwise-busy Monday morning, and how they graciously entertained my wife while I briefed a group of engineers on the latest advances in industrial laser technology.
Along the lines of laser processing technology offshore from the US are four of this month's features: microfabrication process advances in Lithuania (see page 22), airbag fabric cutting in France (see page 12), internal tube welding in the UK (see page 16), and laser sheet metal cutting in Italy (see page 28). These are examples of ILS' global outreach to bring readers the latest in industrial laser material processing.
Also, the cover feature (see page 5) revisits an application that has its roots in pioneering work done when I was director of applications at Avco Metal Working Lasers (AMWL), where our engineers, using a multi-kilowatt CO2 laser, removed anti-fouling paint from submarine hull metal. Interestingly, the author of this feature—Stan Ream—was on the staff at Avco and had left just before this work was accomplished in the late 1970s at the time AWML tried to interest the aircraft industry in the idea, and even got fairly close to the proposal stage with one of the leading commercial airlines.
It seems I have been involved, one way or another, with this laser process ever since that first lab work. In the 1980s, the process got very close to commercialization when some serious investors were prepared to fund a commercial barge-mounted laser paint removal system using a pulsed Nd:YAG laser that was being developed for a military application. I consulted with the team who proposed to use laser energy to remove protective paint from offshore oil drilling platforms in the Gulf of Mexico, and subsequently to develop a land-based mobile unit to remove paint from highway overpass bridges. That came to naught when the prototype laser failed to perform.
Off and on thereafter, paint removal applications cropped up, getting my attention—but as I have said many times, promising laser applications are realized only when the right equipment convinces the using industries that it is ready. Stan Ream explains this in the case of paint stripping.
About the Author
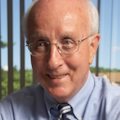
David Belforte
Contributing Editor
David Belforte (1932-2023) was an internationally recognized authority on industrial laser materials processing and had been actively involved in this technology for more than 50 years. His consulting business, Belforte Associates, served clients interested in advanced manufacturing applications. David held degrees in Chemistry and Production Technology from Northeastern University (Boston, MA). As a researcher, he conducted basic studies in material synthesis for high-temperature applications and held increasingly important positions with companies involved with high-technology materials processing. He co-founded a company that introduced several firsts in advanced welding technology and equipment. David's career in lasers started with the commercialization of the first industrial solid-state laser and a compact CO2 laser for sheet-metal cutting. For several years, he led the development of very high power CO2 lasers for welding and surface treating applications. In addition to consulting, David was the Founder and Editor-in-Chief of Industrial Laser Solutions magazine (1986-2022) and contributed to other laser publications, including Laser Focus World. He retired from Laser Focus World in late June 2022.